Monumental Sculpture
Panther-Waxes
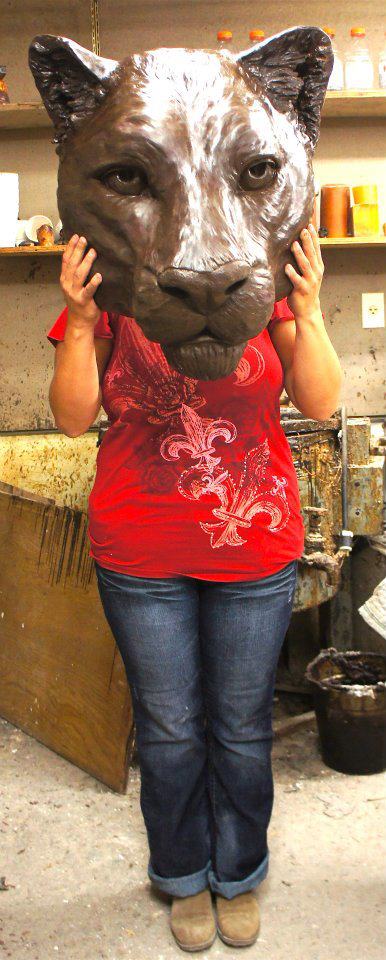
In each of the molds pieces that we made a wax must be poured. There are over 30 mold pieces. Some of the waxes that are poured in these molds will be divided into smaller pieces. Some waxes need to be put together, and all are inspected and worked. Shirley has helped me in the studio and works diligently at the foundry, here she is having some fun with the panther head.
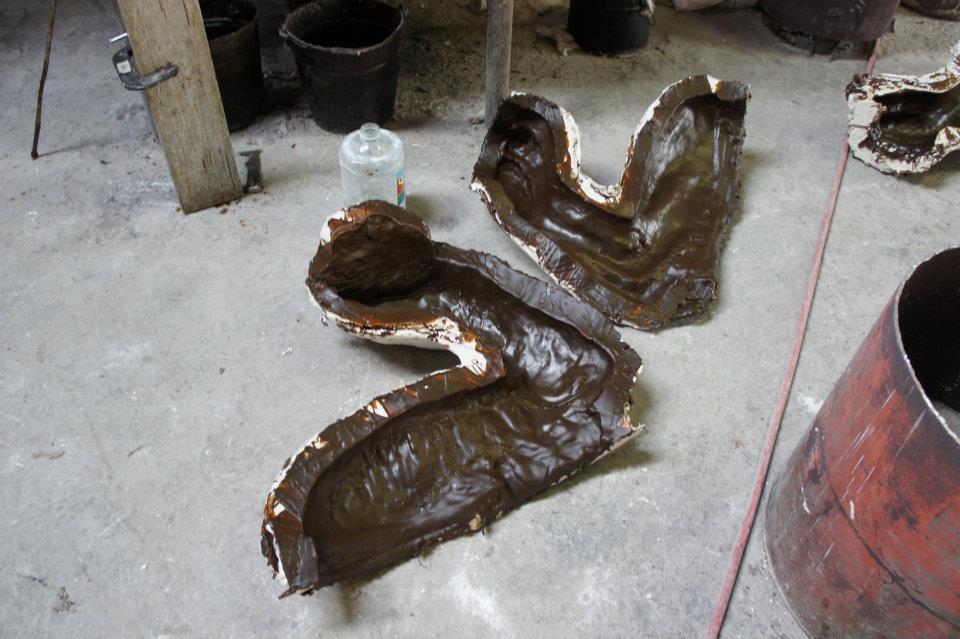
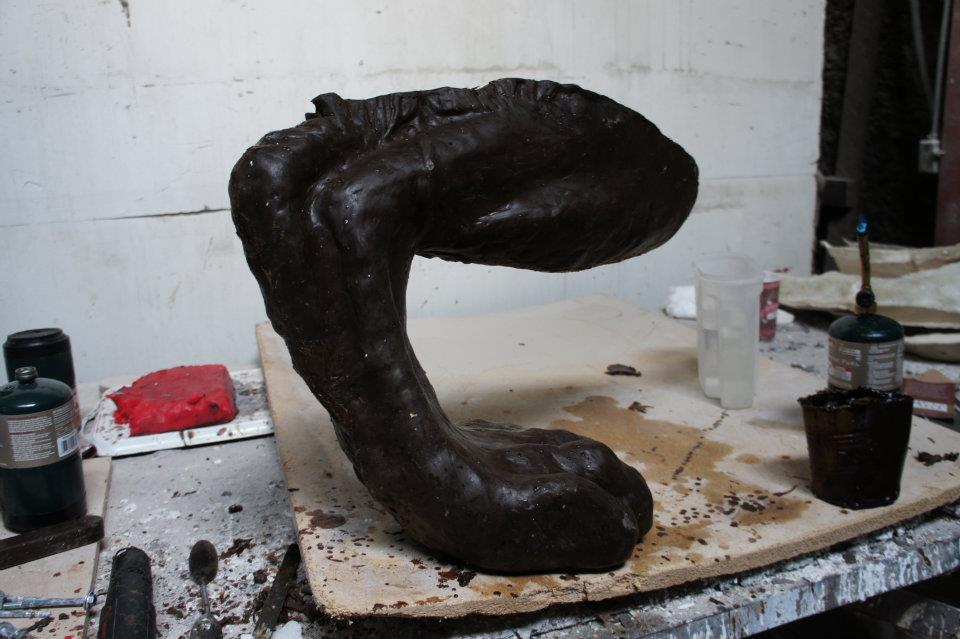
to the next step. It is a lot of work, and our very large panther is in many pieces.
Panther- Going to Pieces
As part of the mold making process each piece must be cut and created into a mold. Some will be done in plaster others will have rubber and plaster. Soon the panther is shedding body parts all over the studio. Days are long and hard starting at 6:30 and going until 10:00 each day with crews switching out when possible. Many foundries create molds, our foundry is requesting we provide them with the mold to expedite the process. We will be feeding them the molds and they will be creating the waxes. There is a crew working in our studio and another at the foundry on the entire process.
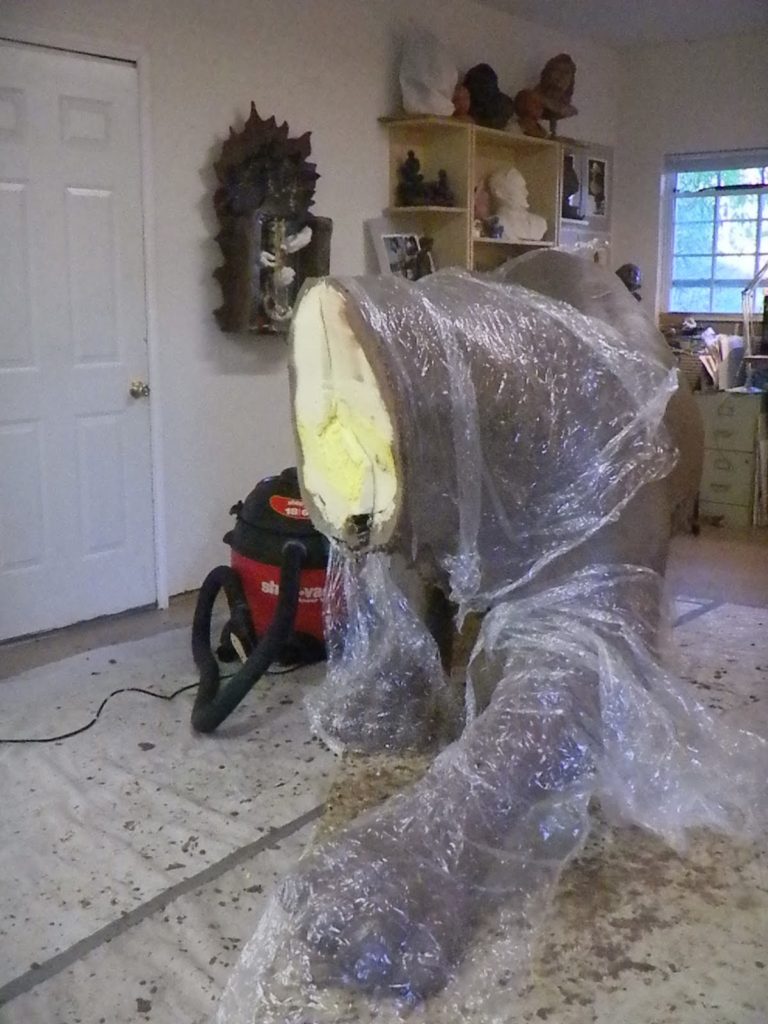
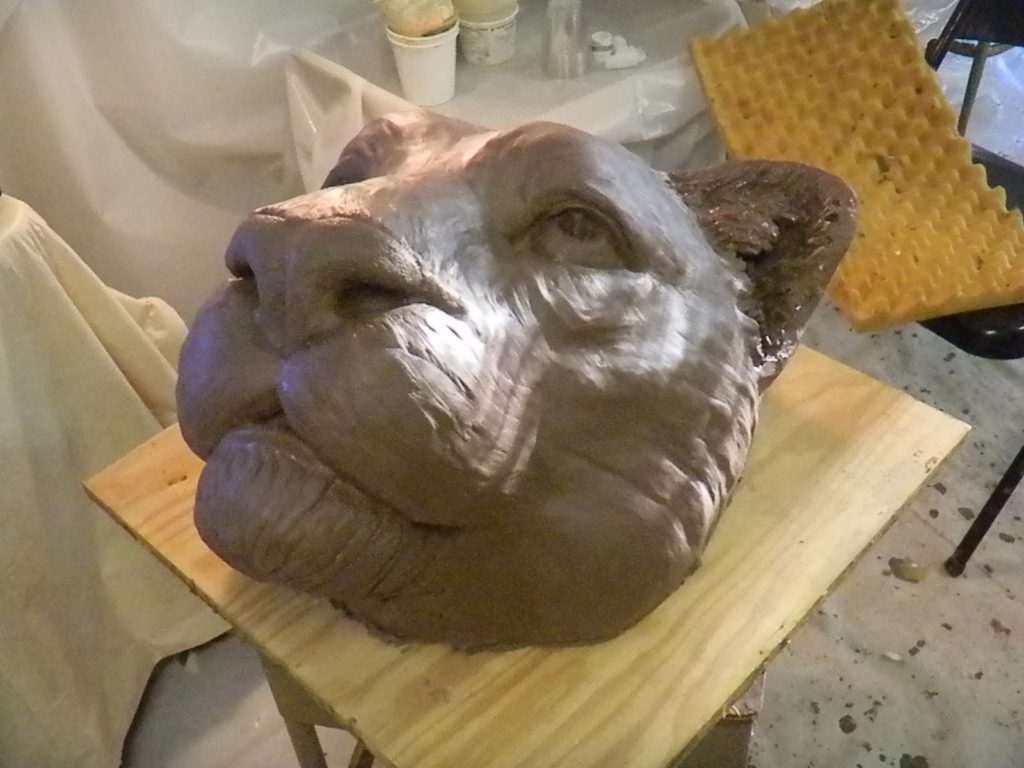
Panther Foundry Process Begins- Mold Making/cutting Up
I lost a day of work waiting for the approval on Friday, and some of my crew can’t work on weekends, but I get started anyway. The first part of the foundry process is making the molds. Believe it or not, the sculpture must be cut up into many, many pieces. Seems a shame, I know, but it is just part of the process. I’m dangerous with a reciprocating saw.

Everyone comes to check out the panther
A group of people from Prairie View have come to see the Panther and approve it. I’m sorry I did not write down everyone’s name. If someone can assist me in this, I would greatly appreciate it.In this picture, artist Bridgette Mongeon, _____, Clifford Stiles, Don Williams, Professor Talley, and Paul Miller the taxidermist.
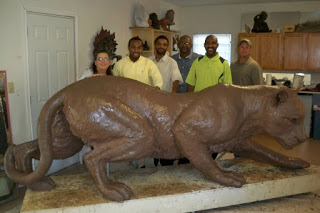
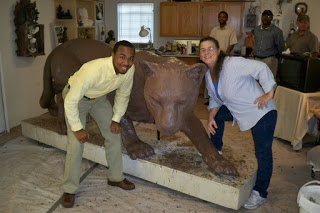
Panther- Final approval
We receive final approval from Prairie View today at 3:00. We have had a crew waiting all day to get going on the bronze process. There is no rushing these next steps. I’ll record them here so everyone can watch what happens.
Panther Changes
There are several changes that are done to the panther. Taxidermist Paul Miller gives me a hand, so that we can meet our deadline. It is a late night, but he is a trooper hanging in there until 2:30 in the morning.
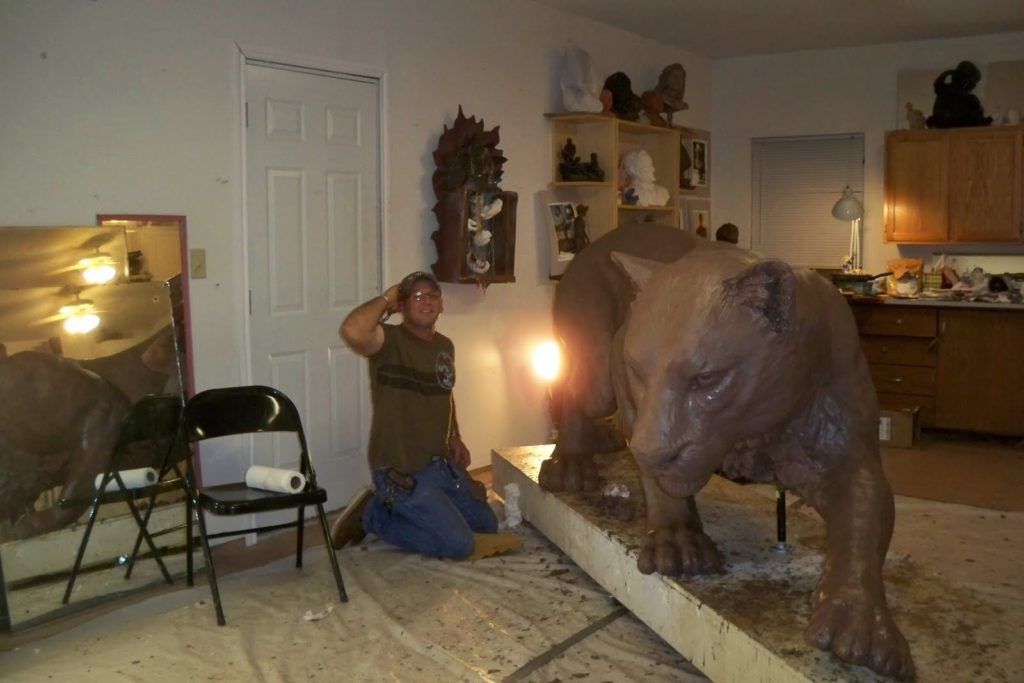
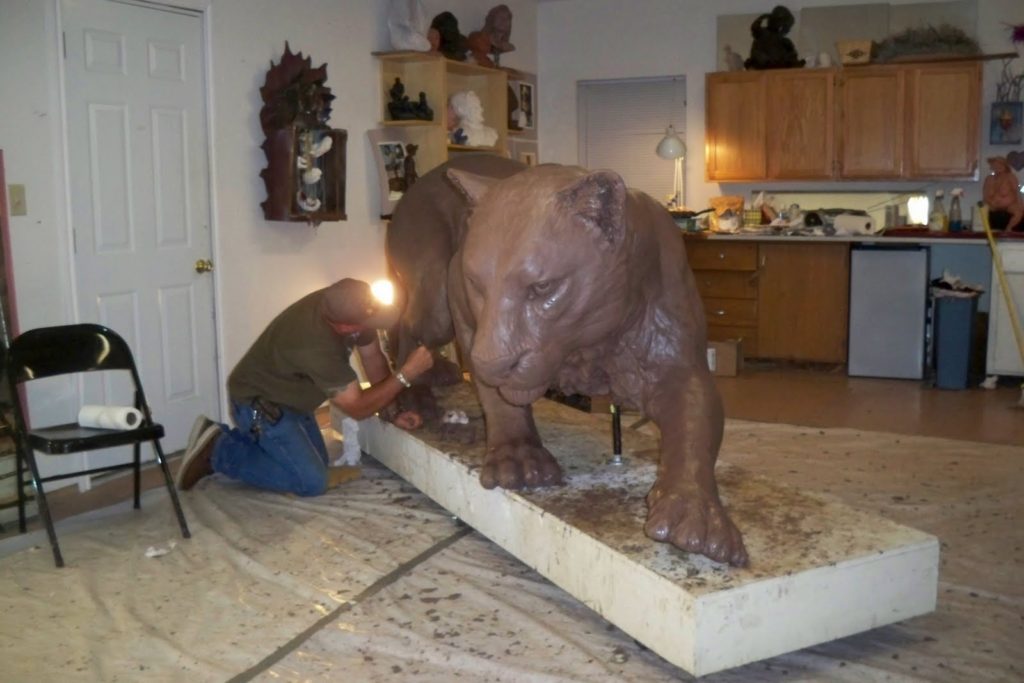
Oh No!
My original deadline was the middle of November. There was a delay in approvals from the college and that put us behind almost 2 months. Then I hear today that the deadline has changed and is homecoming which is the 30th? Oh, my… I’m not sure this is humanly possible. We will do our best. We have finished all that we can and are waiting on the university for approvals. If they don’t get it to us this weekend, I’m sorry, your panther will be missing in action during homecoming.
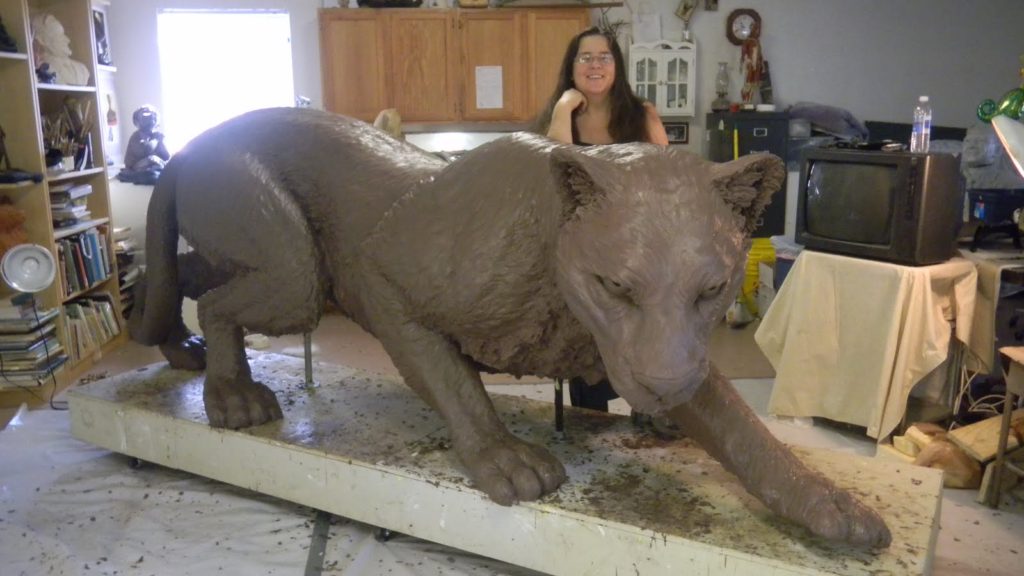
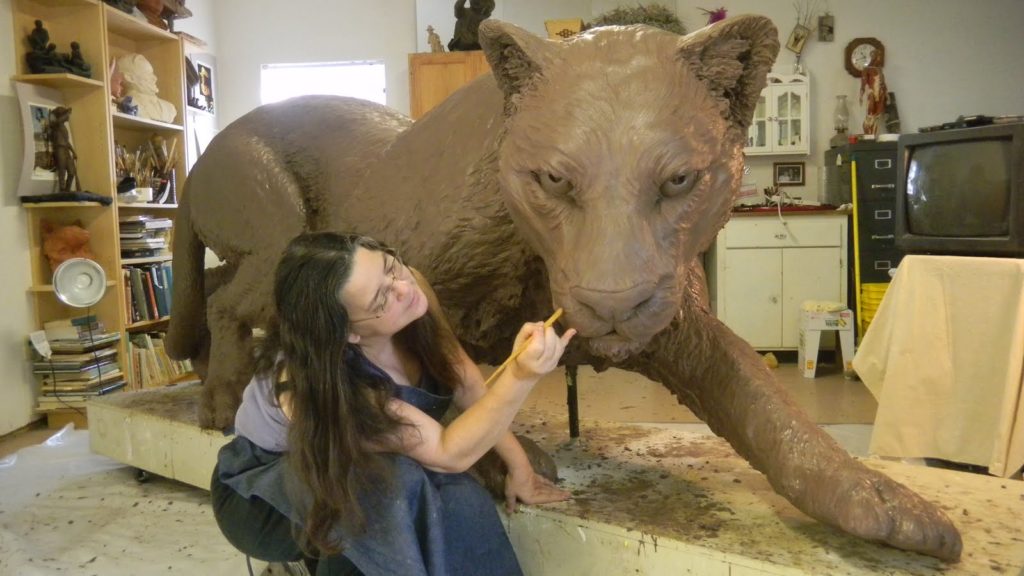
Panther Project- Face Off
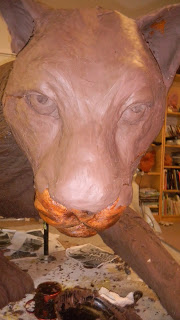
Been working diligently on the face of the panther. Finished late last night. Here are the stages.
This is a sculpture for Prairie View A & M University in Prairie View, Texas of their mascot the Prairie View Panther. The entire process is being recorded on a special blog designate for this project and can be found at http://www.prairieviewpanther.blogspot.com/
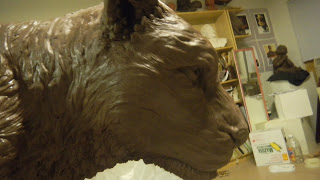
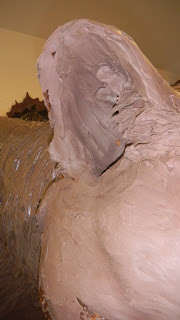
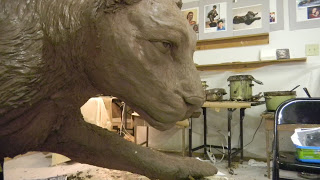
Update- Panther Project- Progress, What Day Is It?
It is a marathon to get this done and approved by the 16th of this month.
Where are those Prairie View Cheers?
I am setting up appointments for the approval of the sculpture for next week.
WHAT DAY IS IT? It is hard to say, my day starts at 6 a.m going into the studio and turning on the crock pots with clay. Then it is a marathon of sculpting until 11:30 at night. Often there is an intern at the studio who is helping me by smoothing things out or adding clay, keeping the crock pots stocked and cleaning up the mess.
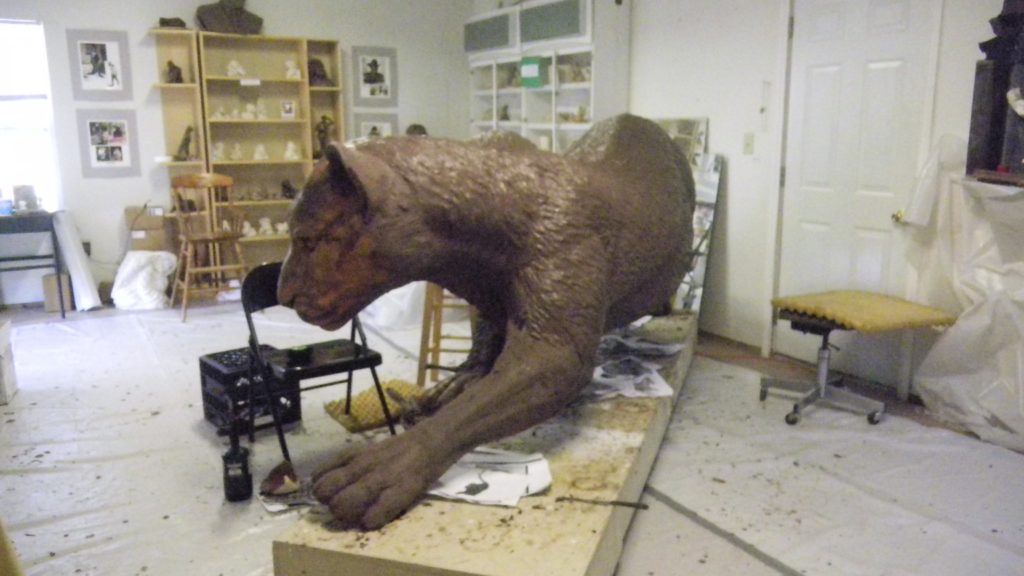
The texture on the cat is taking forever, but I love that it gives the sculpture such movement, it will look great in bronze.
I so want to work on the paws and the head, but I am kind of saving them as a reward for the rest of the work. This weekend. Yes, this weekend, I will get to paws and head.
I’ll post more, but back to getting clay under my fingernails. Check back over the weekend. Do I hear paws? do I hear face? For now it is back to fur and legs.
This is a sculpture for Prairie View A & M University in Prairie View, Texas of their mascot the Prairie View Panther. The entire process is being recorded on a special blog designate for this project and can be found at http://www.prairieviewpanther.blogspot.com/
Update Panther Project- Sculpting Like A Mad Woman


WORK IN PROGRESS- 18 days to sculpt the panther day 4 and 5.
Now that the messy carving of the foam is done the sculpture is vacuumed and brought into the studio. I love this picture of him/her checking out the new digs before entering.There are several people on our Panther Team, all of which I’ll introduce in later posts. You have already met our big cat consultants from the Houston Zoo in another post. I have some pretty diligent helpers trying to assist me in making my deadline. Once the sculpture is in the studio we seal it with wax. This keeps the gritty foam from getting into the clay that will be applied to the sculpture.