Piece of a Panther
Panther- The Pour
In the cavity where the wax once was, molten bronze is poured. Several pours will be necessary to get the many, many pieces of bronze needed for the panther.
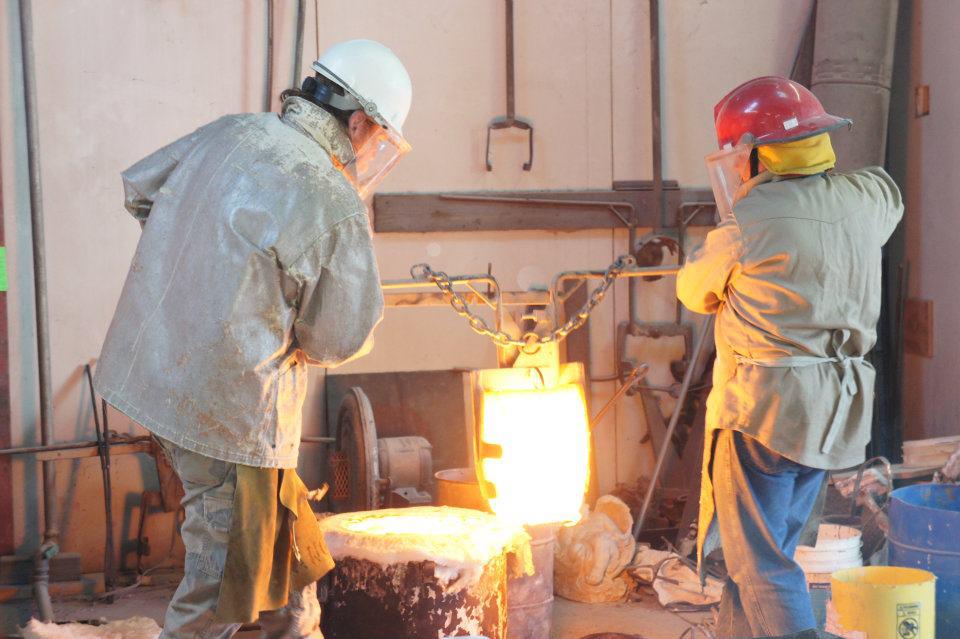
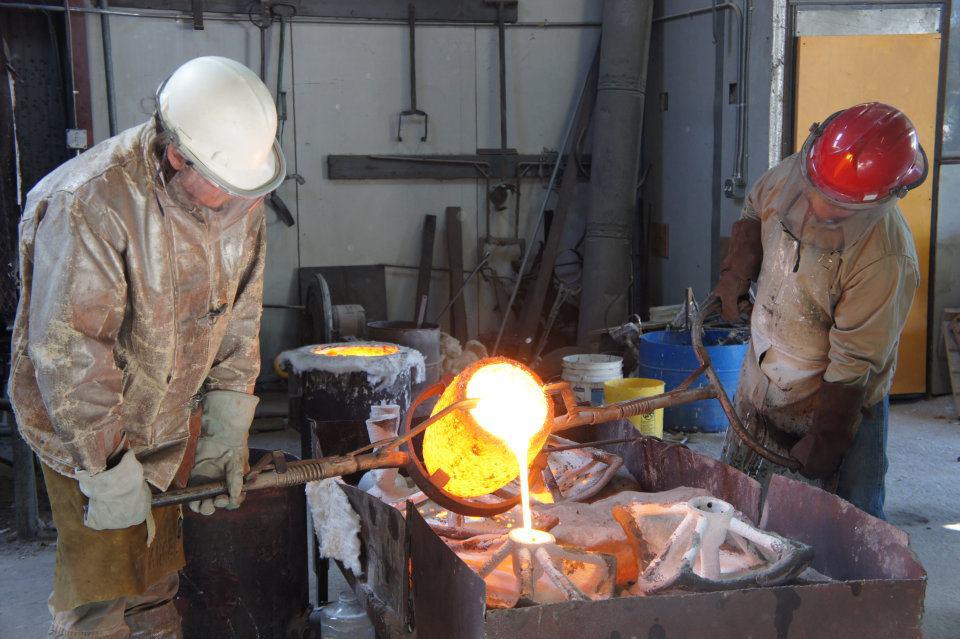
Panther- Burning Out The Shells
Each of the shells is put into a very hot oven and the wax is burned out. Meanwhile bronze is melted in a crucible. In less than two weeks the panther must be together.
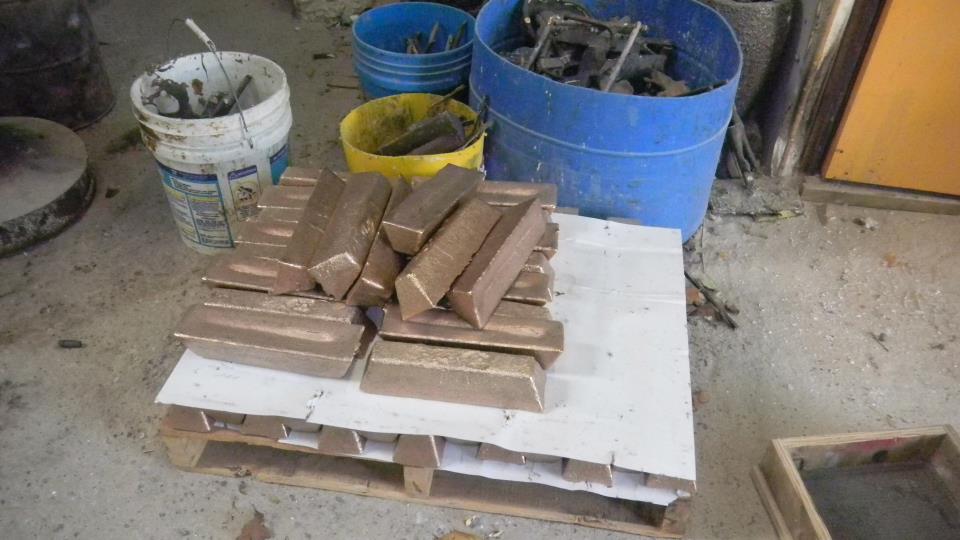
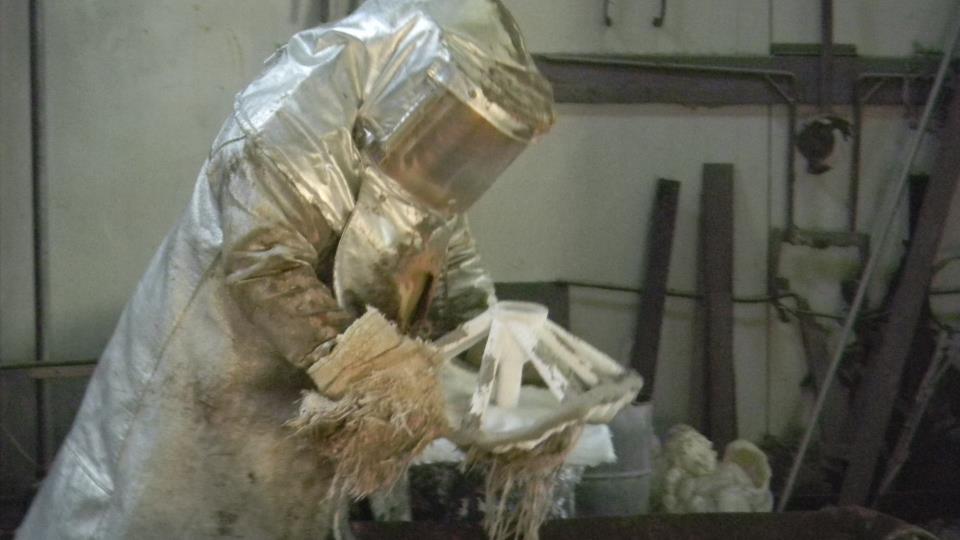
Panther- Dipping The Waxes
Each wax is gated up. That means that they have pour cups and sprues added to each wax piece. The sprues help the gasses to escape when the metal is poured. When they are gated up, each piece is dipped several times in a slurry mixture. There is no hurrying this process. Time is taken to create a good ceramic shell. The ceramic mixture is both inside and outside of the wax pieces.
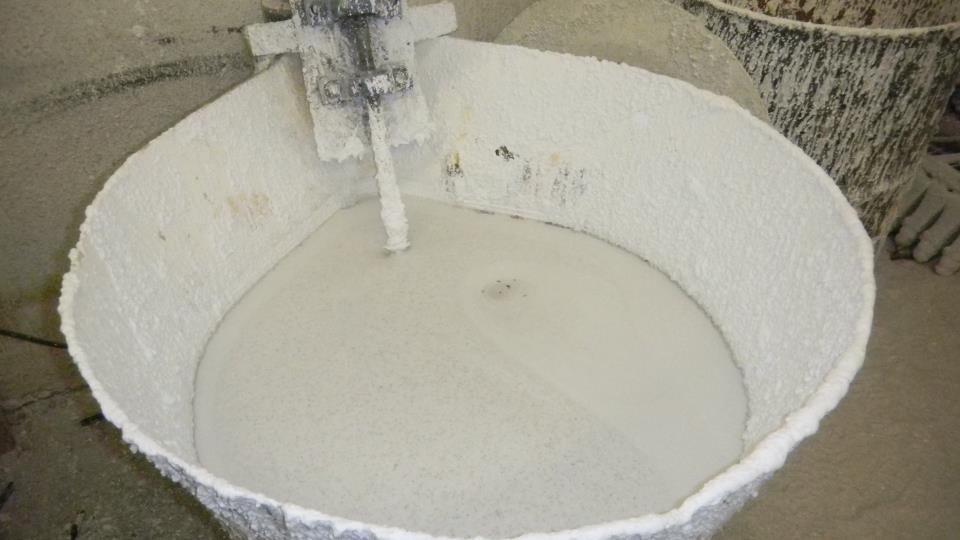

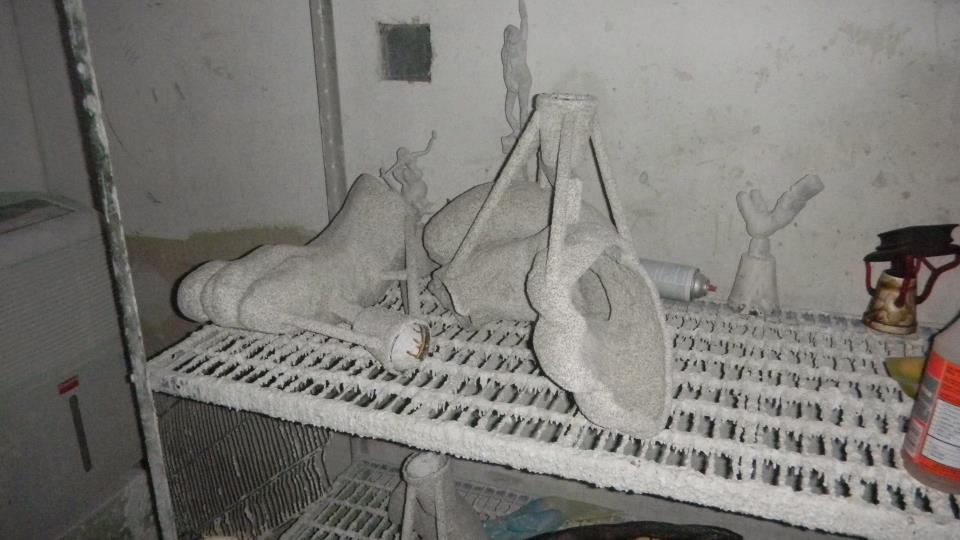
The Completion Of A Project
I have been working on this project for a while now. I really like how it turned out. Some of you may remember I posted about using digital techniques on the creation of this design.
A father commissioned me to creat this for his son as a graduation gift. I love the movement in this piece, there is not a bad side. It is rare that I want to own one of my own pieces, but I really would like to have one of these. Limited edition of 10.
Here are some links to the process.
Working through presentations Daz-Poser-Zbrush- Part 1 and 2
The final results of the presentation using DAz, Poser, Zbrush and Photoshop
Panther-Waxes
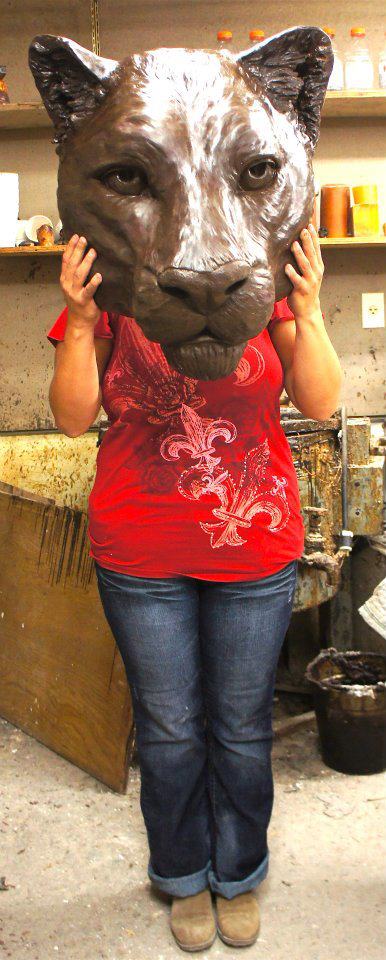
In each of the molds pieces that we made a wax must be poured. There are over 30 mold pieces. Some of the waxes that are poured in these molds will be divided into smaller pieces. Some waxes need to be put together, and all are inspected and worked. Shirley has helped me in the studio and works diligently at the foundry, here she is having some fun with the panther head.
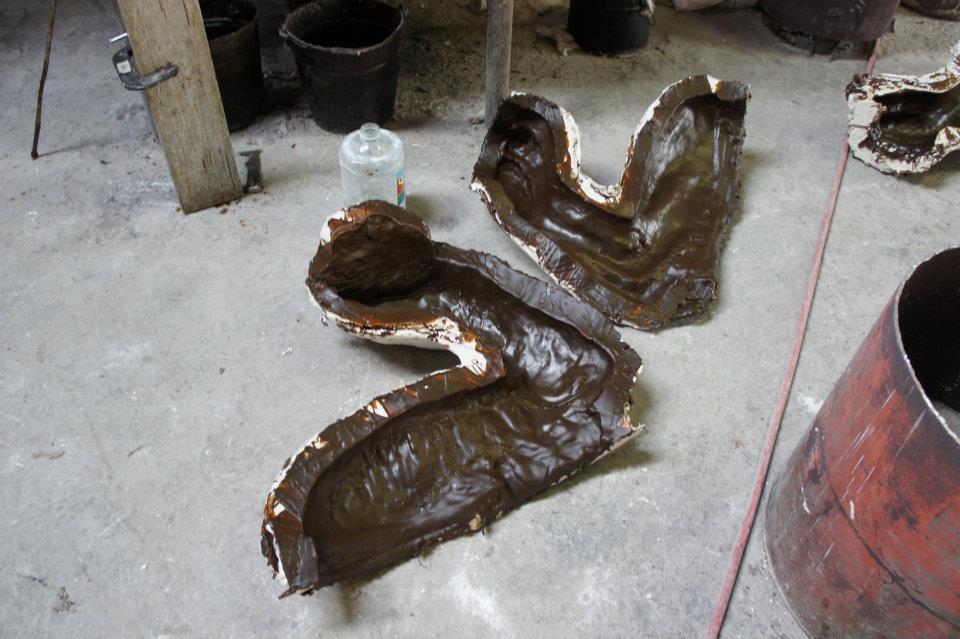
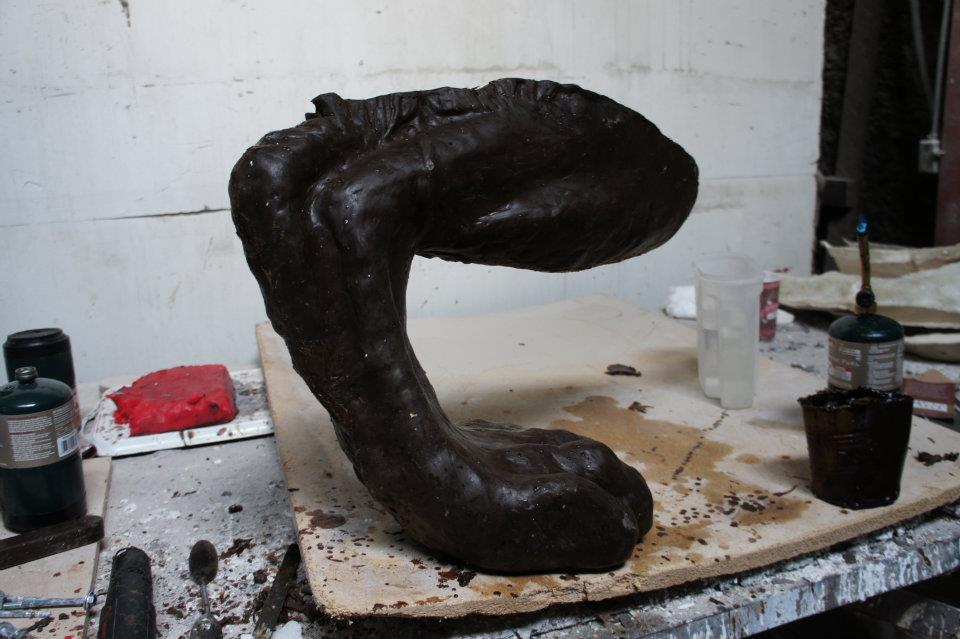
to the next step. It is a lot of work, and our very large panther is in many pieces.
Where Is The Panther?
Many patches of rubber are mixed and applied to the pieces. Slowly we are whittling away at the sculpture. Body parts adorn the shop, while plaster molds bake in the sun and wait to be delivered to the foundry.
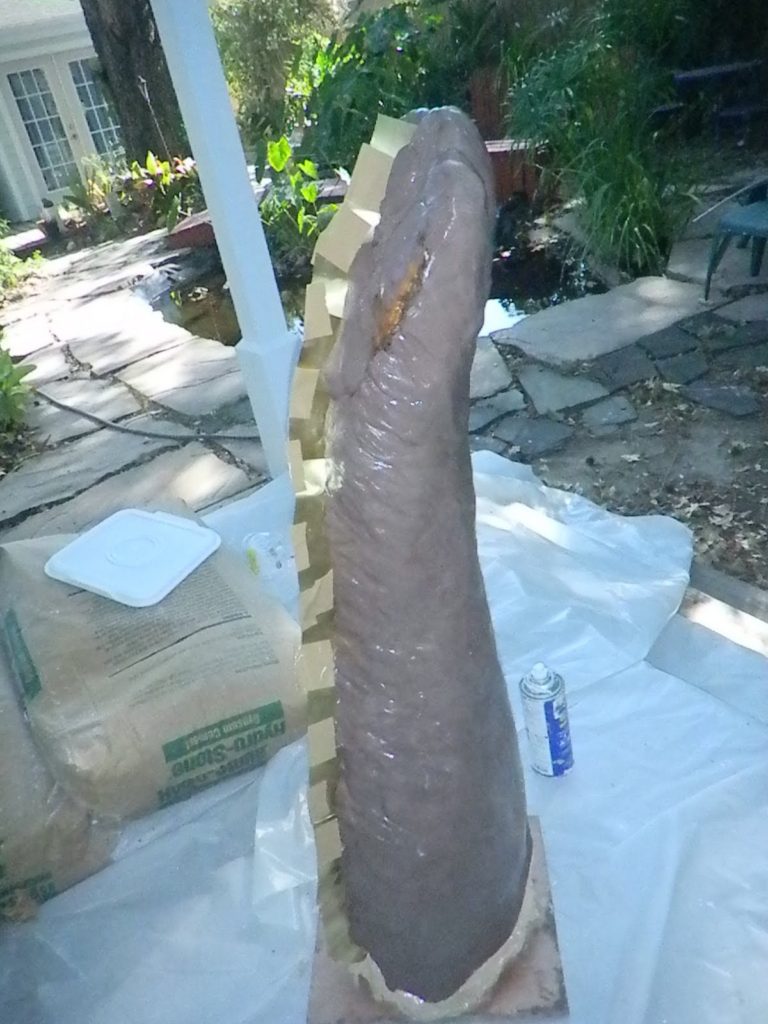
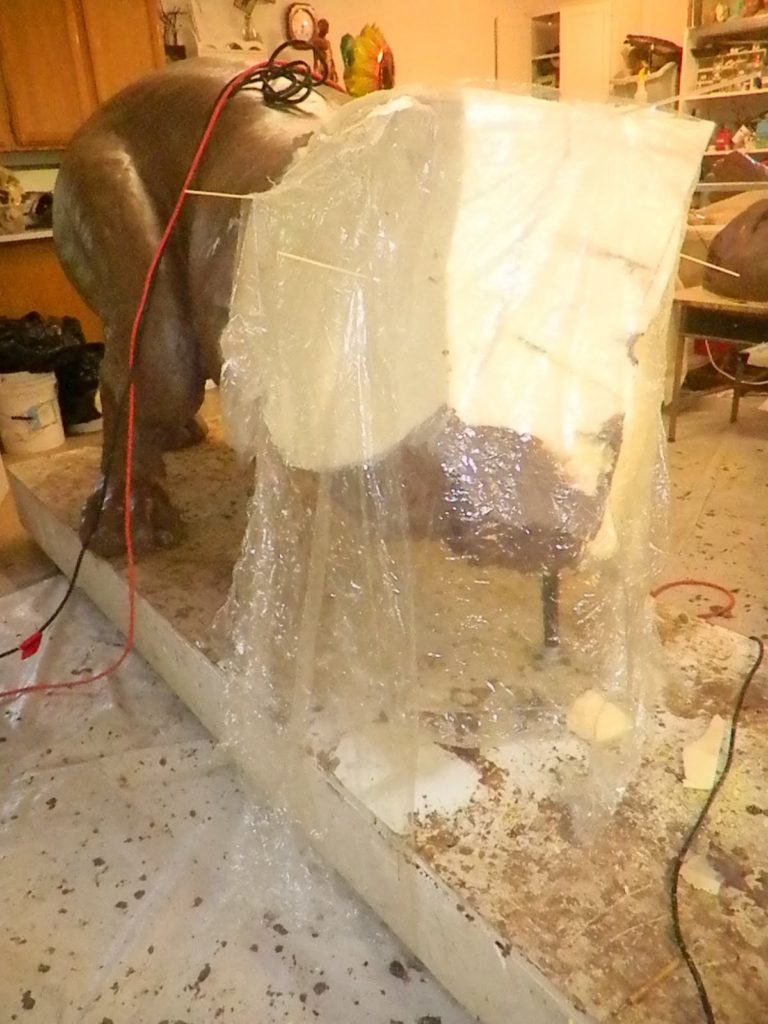
Panther- The First Coats Of Rubber
The pieces, once cut and cleaned are covered in rubber. A mother mold of plaster will be put over these clay pieces. It is called a mother mold because it holds the rubber in place.
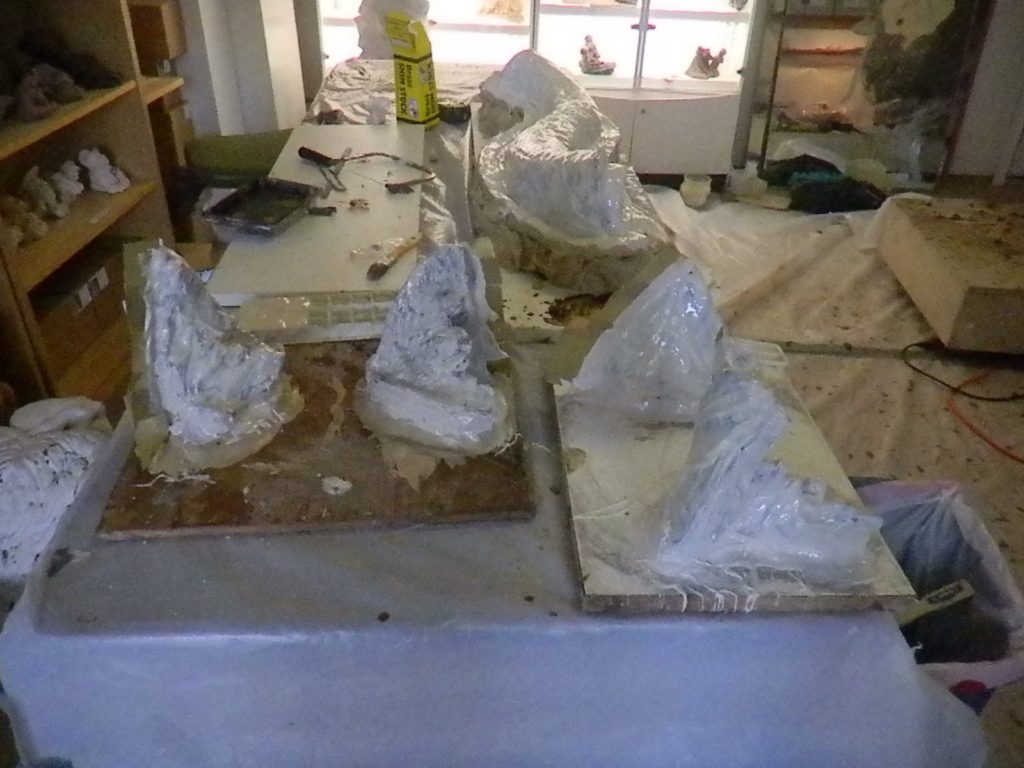
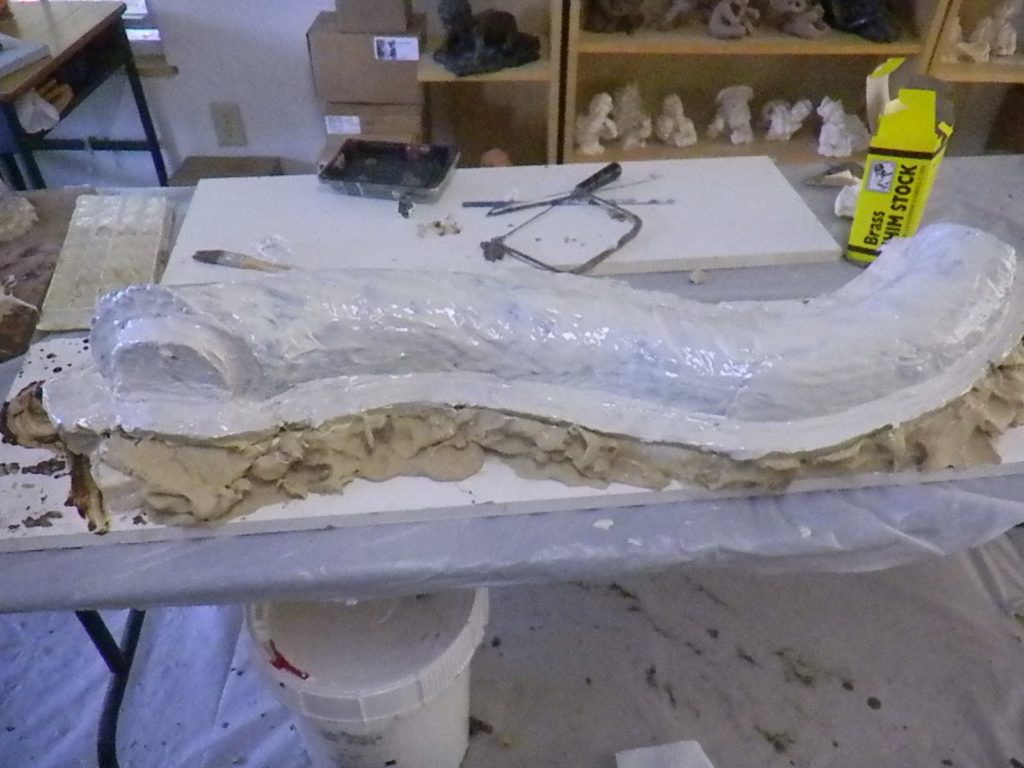
Panther- Going to Pieces
As part of the mold making process each piece must be cut and created into a mold. Some will be done in plaster others will have rubber and plaster. Soon the panther is shedding body parts all over the studio. Days are long and hard starting at 6:30 and going until 10:00 each day with crews switching out when possible. Many foundries create molds, our foundry is requesting we provide them with the mold to expedite the process. We will be feeding them the molds and they will be creating the waxes. There is a crew working in our studio and another at the foundry on the entire process.
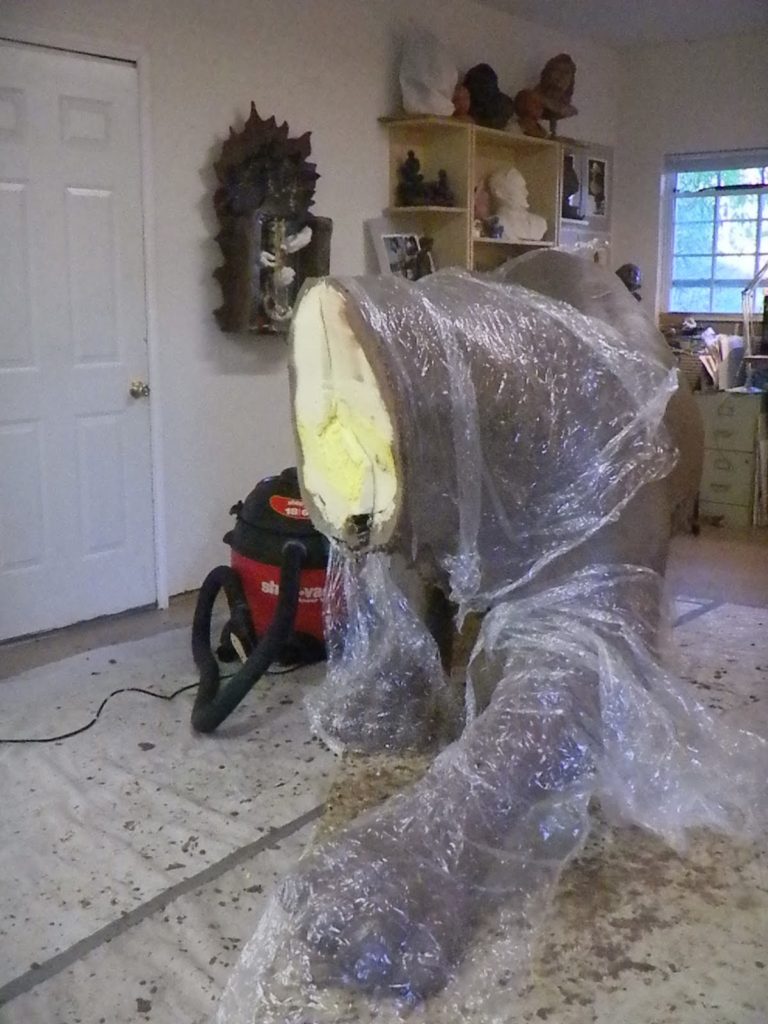
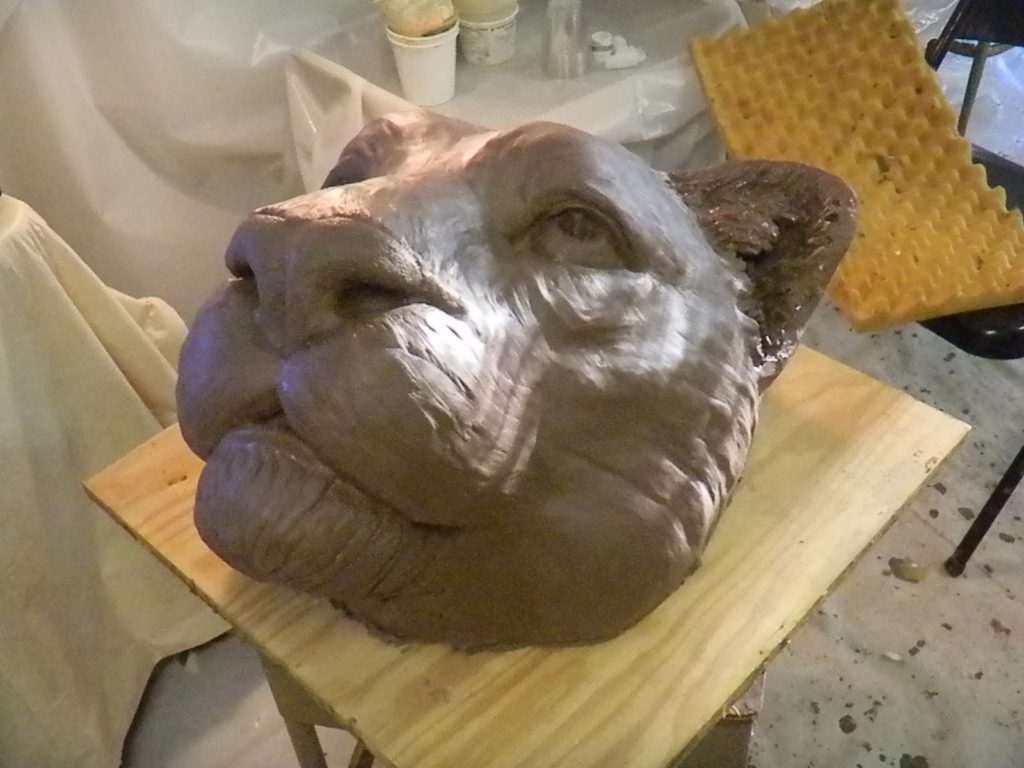
Panther Foundry Process Begins- Mold Making/cutting Up
I lost a day of work waiting for the approval on Friday, and some of my crew can’t work on weekends, but I get started anyway. The first part of the foundry process is making the molds. Believe it or not, the sculpture must be cut up into many, many pieces. Seems a shame, I know, but it is just part of the process. I’m dangerous with a reciprocating saw.
