Writing
YIKES IKE!
Preparations underway for this storm. I’m still headed to the foundry at noon to patina both Dick and Jenna. Then it is back home to get gas for the generator and extra water, plus pick up the yard for the 60-100 mile an hour winds. I don’t like not having electricity but hopefully it won’t be for long. I see the newscasters being cautious in what they say. I wonder if it is because of the disaster of evacuation that happened a few years back. We are staying put, and staying off of the freeways for those who have mandatory evacuation.
GO DEEP TILLY!
I worry that a tree will fall in the pond or worse yet electric lines that are over the pond. Breath and trust God!
OUCH! Oh The Pain
I have over time had difficulty with my hands as I sculpt. Long days of sculpting or mold making can cause considerable pain. That is why I love my apprentices! My husband and I went to listen to some jazz and we met a physical therapist who sat with our group. She kindly worked on my hand and arm. Maybe it was the wine, or the Advil, but most likely it was her massage. It could have even been that I danced my feet off. Whatever, it felt better when I got home, I iced it and the next day I vowed I would wear the brace all day while I work, but first created a sleeve of a large latex glove over the hand/arm.
I had to cut the fingers our of it. It is amazing how much the tactile sensation I long for of the materials that I use that help me to complete my job. Now I am thinking about learning to tape up my hand like a sports player.
Rest… that is what everyone says. But my other job is a writer. So fingers are still going. It hurts to hit the space bar. And my favorite thing to do for relaxation is gardening- more fingers.
I Have My Approval On The Surprise Christmas Gift

Portrait sculpture is a great gift to give someone that has everything. That is what this lovely wife said as she approved the sculpture of her husband on Saturday. I’m pleased to have my approval. A few corrections to details and now it is on to the mold and metal for this sculpture. We must be done for the Christmas party.
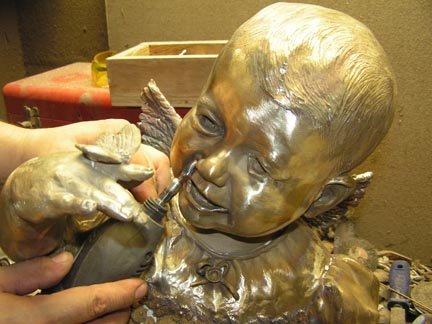
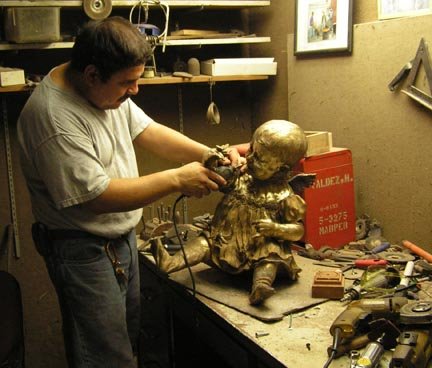
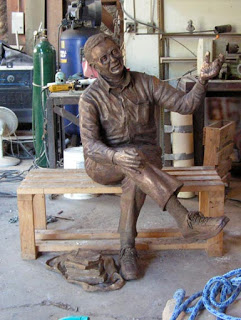
New Article- Best of Artists & Artisans
There is a new article posted at the Best of Artists and Artisans blog titled
Mold Making and Bronze Casting-Part I . For those interested I have listed suppliers and materials. The article goes along with the recent video created of the Richard Hathaway Memorial Sculpture.
A Review of New Technology For The Traditional Studio at the SIGGRAPH Convention
Writings by Ms. Mongeon
Created for Best of Artists and Artisans web site
By Bridgette Mongeon © 2008

Using technology in a traditional art studio can, at first, feel like cheating or it may bring a fear that the technology can somehow overtake the craft and creativity. I mentioned these fears and my introduction to this topic in a recent article titled Exploring Digital Technologies as Applied to Traditional Sculpting– Sculpture Review Winter 2007. In the article, I explored incorporating digital scanning and milling in the traditional sculpting studio. My research alleviated my original concerns and fears as I realized that digital enlargement, though a little intimidating at first, can be combined with traditional techniques offering another tool to use in my creative process, a tool that has the added benefit of providing me with more time to create.
I continued my research into utilizing technology in the traditional art studio while attending the 2008 Siggraph Convention this past August. Siggraph is short for Special Interest Group on Graphics and Interactive Techniques.
I once considered Siggraph as a convention for those working in graphics since it relates to illustration or computer generated special affects for movies. I have watched with curiosity over the years as the technology that has been introduced at Siggraph has infiltrated the 3D world outside the computer and into traditional sculpture studio. Those at Siggraph also seemed to be embracing the idea of bringing technology into the art studio. Three prime areas, besides the main floor of exhibitors, displayed this same exploration.
THE STUDIO
The Studio section hosted six established and emerging resident artists, along with hands on participation for learning and creating in 2d, 3d, and 4d (fourth dimension is time.) Though The Studio contained quite a bit of resources, two visiting artists captured my attention.
Matt Shlian calls himself a paper engineer, creating elaborate sculptures through the use of folded paper, which is not to be confused with true origami because he cuts and glues. My intrigue with the art was that many of the forms generate movement, changing shape with the interaction of the viewer.
It is interesting to point out that many of the artists I researched who were working with technology in their art also crossed over into the area of science. A segment of Matt’s website states this.

“As a paper engineer my work is rooted in print media, book arts and commercial design. Beginning with an initial fold, a single action causes a transfer of energy to subsequent folds, which ultimately manifest in drawings and three-dimensional forms. I use my engineering skills to create kinetic sculpture, which have lead to collaborations with scientists at the University of Michigan. We work on the nanoscale, translating paper structures to micro origami. Our investigations extend to visualizing cellular division and solar cell development. Researchers see paper engineering as a metaphor for scientific principals; I see their inquiry as basis for artistic inspiration.”

Another person that caught my eye was metal smith and jeweler, Sondra Sherman. I told Sondra that my goal as media at Siggraph was to find artists who were bringing technology into their studio, and she made sure that I knew that her present designs were created by hand, but that learning about the technology that would apply to her art studio was also her goal while at Siggraph. “I believe artists in craft media are always curious about means or materials which might enhance or facilitate their creative expression and which seduces the viewer to engage with the work. I am not interested in the ‘novelty for its own sake’ quality, which the use of technology might bring to my artwork. I am interested in how I might use the attention given to novel forms/materials to attract the viewer to consider what I might be trying to express with that form, as they would with work created in any media or by any means.”
SLOW ART
Slow Art was a juried exhibition. Artists were asked to “reconsider the paradigm of speed and instead consider the concept of “slow art.”’ The questions that were raised— how do you employ speed afforded by technology, how does it affect the work, and the process of creating slow art?
There were a variety of pieces of art in this section that peeked my interest. One of mention was an interactive piece that is the literal description of slow, titled —RealSnailMail. In this exhibit you send an e-mail on a designated computer in the slow art exhibit. It is then sent to a server in the UK. Here the e-mail is in a holding pattern along with the many other e-mails as it waits for a snail equipped with a transmitter in a tank at Bournemouth University, UK, to slide into range of a hot spot that can pick up your message. It then must move to another area of the tank to send it.
I could not help but wonder just how long my snail mail would take to get to a person. I emailed Bournemouth University in the UK using the regular fast e-mail and they quickly replied. “We have done a bit of calculating this morning. As of the 8th of Sept. 2008 we have 8,977 emails waiting. Based on this, if you sent an email today, it would take 24 years, 217 days before it gets to the front of the queue. It then may take a further 69.87 days (average snail transfer time) before being forwarded to its final destination. Therefore, a RealSnailMail sent today should arrive approximately by Thursday 16th of June 2033. Please note times may differ dependent on snail behavior and usage.” Now I am wondering how many people will have their same e-mail address twenty-four years from now.

Interaction seemed to be the theme through the entire Siggraph convention. The question was, which sense was going to be stimulated or interacted with, by the art or new technology? Another one of my favorites in the Slow Art integrated vision, touch, and sound. Joo Youn Paek’s Fold Loud was a visual of large sections of tapestry incorporating origami shapes that could be folded, and in doing so, they opened circuits made of conductive material creating harmonic vocal sound.
It was difficult to truly appreciate the Taoist principles intended with this soothing art while standing in a noisy convention hall, and I was glad to see you could hear the work by visiting the Fold Loud website. I loved the opportunity to interact and touch the sculpture and while doing so to also create my own meditation.
DESIGN AND COMPUTATION
The third area depicting art and technology was the Design and Computation section of Siggraph. Here artists, designers, architects, and mathematicians created artwork, images and structures utilizing technology in both design and digital fabrication.

I had many favorites. The two pieces I choose to focus on were not figurative at all but instead were once again patterns and shapes.
It might seem strange to see the work of a traditional veteran sculpture like Erwin Hauer in the technology exhibit at Siggraph. Hauer created works of modernism that began in 1950 and can be found, not only in museums and collections but also in architecture. The patterns in Hauer’s work held the same intrigue that Shlians paper cutting held for me in The Studio section of Siggraph. Each modular constructivism sculpture of looping forms change as the viewer interacts with the piece, light bouncing off form, shadows moving and blending, creating an entirely different piece of artwork from every angle.

A book of Hauer’s work titled CONTINUA was published in 2004, but it is said that by that time of publishing many of the existing screens had disappeared or were in disrepair, and the laborious task of making molds and casting these screens had not taken place in nearly 40 years. In 2003 computer technologist Enrique Rosado began working with Hauer creating digital files of Hauer’s original work, CONTINUA. Utilizing the new technology of digital files and Computer Numerically Controlled (CNC) milling machines, the team is working to recreate the works of this master.
The journey of translating the designs into the new technology was not easy for Rosado. He found what I have found in my research; often you must push the technology to do what you need it to do, and then wait until it can catch up and become affordable. In a wonderful magazine article about Hauer’s work in Metropolimag.com it states, “These subtleties of balance and proportion were difficult to translate into the software. ‘The computer wants to do what it wants to do,’ Rosado says. ‘And if you’re fastidious, you really have to beat it into submission.”’
My other choice in Design and Computation was actually a student of Hauer. Bathsheba Grossman says that she was an undergraduate at Yale studying math when she first saw Hauer’s work. It was life changing; this is what she wanted to do. After graduating with a degree in math she went on to study sculpture at University of Pennsyvania. Bathsheba transfers math and science into wonderful sculptures utilizes 3D printing in metal and 3D laser etching as the output. She reports that her “traditional” studio has been reduced drastically, as she creates most of her work in the computer. It is because the complexity of her work cannot really be done any other way. She creates in a space that is inaccessible to traditional forms. Immersed in technology, for years she has watched as some traditional artists like jewelers begin to gravitate to working on screen instead of through tiny loops. It is not without its sacrifice, as she admits there is a tactile experience that is the reward of creating manually.

She waits patiently for technology to catch up to her needs as an artist. I learned that the “rough” texture created in the very intriguing process of digital printing in metal is a result of the technology and not part of her design. She is waiting for technology to improve. For those artists pursuing technology in the studio, it may sometimes feel like it progresses at the pace of RealSnailMail.
There were many more discoveries that I have found at Siggraph, which I hope to share in this column in the coming months, along with some wonderful tutorials on the advances in digital technologies as it pertains to the traditional artist. I myself have decided to embrace the technology and share it with as many creative people as I know. Maybe this will increase the snail’s pace and create the demand for the advances in technology that will assist us in our future creations. Though technology is improving and it will help us; in closing I would like to leave you with a quote from Hauer,
“It is an important token reminder for the younger generation and their tutors, that above and beyond the abundance of electronic marvels, the human vision and imagination remains the most important element and that its nurture should not be replaced by excessive reliance on devices.”
Mold Making and Bronze Casting- Part II
Created for Best of Artists and Artisans Website
By Bridgette Mongeon © 2008
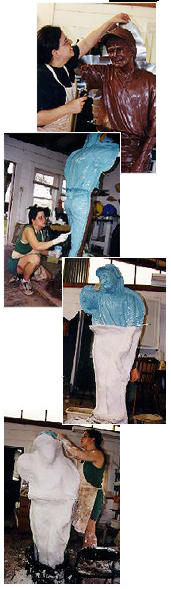
THE MOTHER MOLD
In the previous article Mold Making and Bronze Casting-Part I, we learned about preparing your sculpture for the mold making process and painting rubber on the sculpture. If you want to see a mold being made please refer to the video, The Casting of the Dick Hathaway Memorial. The video has been embedded in the online article Part 1. I will refer to this video often in this article. In Part II, I would like to talk about the process of creating a mother mold. Once this portion of the mold making process is complete, your molds can be cleaned, sent to the foundry, and waxes can be poured into the molds. Your artwork then begins its journey through the foundry process and through the lost wax method of bronze casting.
Mother molds are called mother molds because they hold the rubber in place. Your rubber may have been created in two or more pieces or sometimes one piece with a seam up one side, but a mother mold must be able to be pulled off the artwork, and it will not have the flexibility that rubber has. To be able to take the mother mold off the sculpture, it may entail visually dividing your sculpture up into more sections for the mother mold so that the pieces can be pulled off without any force or prying that may destroy the wax that will be poured into the mold later at the foundry. Drawing with a marker on the cured rubberhelps to define the mother mold sections. You will “clay up” seams, just as with the rubber portion discussed in Part I, claying up the sculpture along these marker lines in preparation for the plaster.
NOTE: You must “clay up” before putting on the mold release, or the Klean Klay will not adhere to the rubber. To make the Klean Klay adhere warm it up in a microwave as in the rubber stage and push it onto the dry rubber. Thicker “clayed up” seams are preferred over thin seams in both the rubber stage as well as making the mother mold seams. There is nothing worse than having a clayed up seam break loose while making the mold.
Mother molds can be made in a variety of different products. Most artist use a type of plaster called Hydrastone. Hydrastone is much stronger than Potter’s Plaster. You may be able to purchase Hydrastone from your art dealer, but most likely it will cost more than getting it from a supplier. I purchase mine from Circle Supply in Houston, Texas. A 100-pound bag of Hydrastone at Circle Supply costs $32.89. I went through three-100 pound bags on the Dick Hathaway sculpture featured in the video.
Mother molds can also be made in fiberglass. If I know I will be creating many pieces in an edition and I will need to obtain many waxes from a mold, I consider the extra effort of using fiberglass. You will be quite surprised how heavy a small mold can be with a mother mold of plaster. Fiberglass has its advantages for larger molds as well, because upon completion the mold is lighter. Fiberglass is, however, I believe, difficult to work with and toxic to use.
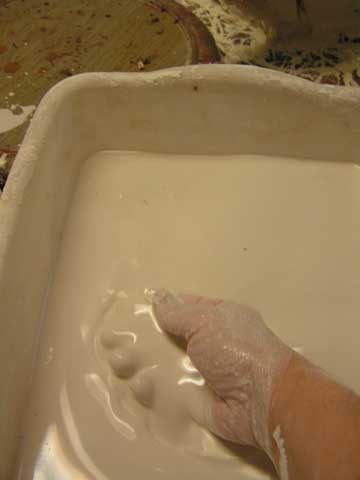
The plaster portion of the mold making process is the messiest part. In the past, I have fooled myself into thinking, “Just let the plaster fall on the floor and it will dry and scrape up easily.” This is just not so, and preparation of my space for making the mother mold is just as important as the rubber. It also makes clean up so much easier.
I usually like the rubber to cure a day before putting on the plaster, and often the plaster is done in conjunction with rubber. For example, if a mold is done in two pieces like the leg or arms in the video, I will paint rubber on one side then put the mother mold of plaster on top of that, and then flip the sculpture to do rubber and a mother mold on the other side.
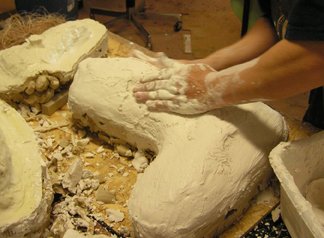
Before beginning to put the plaster on the rubber, you must note there is a process of preparing the rubber so that the mother mold can be pulled off the rubber. I mentioned this in Part I. This step is done in the rubber stage. This part of the process is not shown in the video and is a bit tricky to describe. Pieces of foam, the kind of foam that is in your sofa cushions, have been stuck to the rubber in areas of deep undercuts. Then a skin of painted rubber is put over the foam. The foam offers the “give” that the rubber mold needs to fold back on itself as it is taken off the wax that will be poured into the mold. It also gives a flatter surface with no undercuts for the plaster mother mold to be put on top. I will try to make a video or take detailed photographs of this the next time I make a mold.
Before applying plaster you should cover your rubber with a mold-releasing agent. An inexpensive source for this is simply using shortening such as Crisco or a store brand purchased from your local grocery store. Rub this over the entire surface. Putting your hand inside a plastic bag first helps to coat the rubber without making your hands gooey, an old cooking tip.
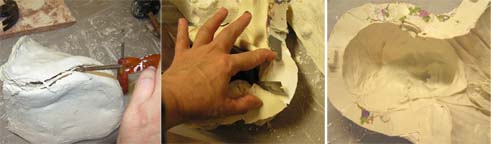
I usually have four plastic buckets, one that I am mixing in, one that holds a bit of hemp soaking in water, another that has extra plaster, should I need it, and another for washing my hands.
Mixing plaster is tricky, and you must watch it closely because when it activates there is little time to work. Working on smaller areas is much easier than a very large area. Be prepared to get dirty.
HINT:The Hydrastone makes these containers weak. I figure it must be a chemical reaction. Plus, I will often bang on them with a rubber mallet to get the hardened plaster out. When using the last bit of mixed plaster in the container, or if there is excess, try to scrape to the bottom in the center of the container. Then after the Hydrastone cures in the bottom of the plastic bucket, I can bang on the container freeing the two pieces into the trash can outside my studio and offering me a clean container to use for the next part of the mold. You will have to find just the right spot to bang on the container to loosen the plaster form the container without plunging through and breaking the increasingly brittle plastic. I prefer the rounded edge of the bottom.
HEMP: I purchased a bale of hemp, which will probably last me a lifetime. I might suggest you talk to your foundry or another artist and see if you can purchase some of their hemp from them. Be careful, if you buy a bale and clip those metal straps around the bale, the thing will explode, and you will be trying to figure out where to store all that hemp.
DO NOT MAKE A MOTHER MOLD WITHOUT HEMP. If you break your mother mold you have lost your piece. Hemp increases the strength of your mold, and if you are in a hurry, like I usually am, you are going to want to get this mold pulled and into production as quickly as possible. Molds, just after their completion, can be quite fragile.
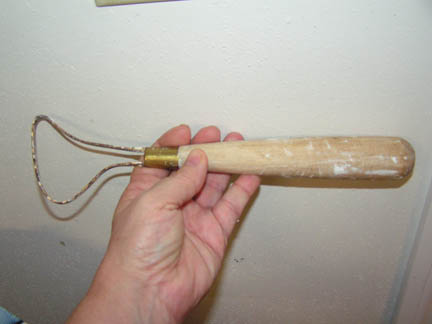
Fill your plastic bucket with water to the amount needed for the amount of Hydrastone mixture you will want to use. I am not sure how to tell you how much to use; this knowledge will come with practice. Always mix the Hydrastone into the water. I start by making mounds of Hydrastone and letting them soak. You can get ratios from your Hydrastone supplier, but I really do this part by sight. Usually I add a bit more Hydrastone as I impatiently wait for the bucket to begin to “kick”. I mix all my plaster by hand and don’t use any mixers. This really helps me know the different stages of the plaster. It is something I do by feel. While the Hydrastone is soaking, I’ll take some of the hemp that has been soaking in water and arrange it over the rubber section that I am about to cover in Hydrastone, being sure to put some on the seam area. Then I will take this hemp off and dip it into the Hydrastone mixture and lay it back on the rubber. As the mixture begins to “kick”, I must work quickly, putting the plaster on the sculpture, forcing it into the hemp and building the areas that I need, including the seams. I strive to make the entire mold an inch thick or less.
When you are finishing the Hydrastone mother mold section and the Hydrastone is curing—you will know this is happening because it becomes increasingly warm, go over the section one last time with a wet hand to “polish” the outside surface of the mold, making it smooth.
HINT: When creating a section of mother mold next to another section of mother mold, I also rub the Crisco or cooking shortening on the edge of the completed Hydrastone piece. This will help in separating the pieces and keep splashes of Hydrastone from being stuck to the already hardened plaster.
There are a couple of tools that I think are necessary to create the plaster. For example, I love having this large loop tool around when creating my Hydrastone mother mold. It is great when you want to clean up your Hydrastone seams and not make them jagged. This tool also cuts through the Hydrastone, even after it begins to cure, which is helpful, if I feel I have too much Hydrastone in one place.
Once all parts of the plaster are made you will want to separate the mold. Waiting a day or two for the Hydrastone to cure is helpful. It will take longer in high humidity. As the water evaporates from the Hydrastone, it will strengthen and will become a bit lighter.
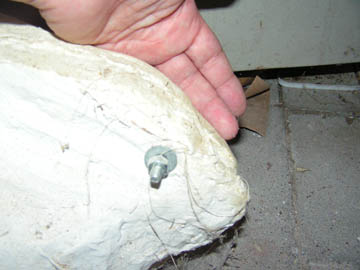
HINT: Small molds are often held together with rubber bands, larger molds may require bolts. Making a seam that comes up at the edge provides room for bolts. These bolt holes can be drilled before pulling apart the mold. Be careful not to jeopardize the rubber underneath. Often there is so much rubber and plaster, it is sometimes hard for me to make out where the sculpture actually lies underneath.
Separating the shell can sometimes feel like an impossible endeavor. I have several screwdrivers that I can shimmy into the seam. Once one is in a seam, I’ll try to move it down a bit and put another in, doing the same thing all of the way down the seam, being careful not to puncture the rubber underneath. More than once I have to struggle with a seam, only to flip the mold over and try another one. As a l ast resort, I may try to scoop out the clay from the open section where the wax will be poured, giving me something to hold on to, and I use this to pry the pieces apart. It takes practice to know when and where to apply pressure and when not to. This part of the process can take a good deal of strength.
NOTE: Be very careful if you are prying one piece of Hydrastone off another. It is easy to shatter a corner or an edge. Go slow and steady, and if you feel frustrated walk away, get lunch, and come back later.
Once the mother mold is separated, you can pull the rubber away from the original art. You will lose the integrity of your original art, but I keep the sections, especially the face. Should the wax come back to me and not look right, it gives me something to compare the wax against. Before sending these molds to the foundry, the rubber will need to be washed both inside an out. This can be done with kitchen soap and a good brush. Sometimes a toothbrush helps to clean small textured areas. When cleaning the inside, be sure that all the clay debris is out of the crevices and details, as this will be picked up by the wax, rendering the wax unusable.
The Crisco should also be washed off the outside of the rubber. Then the rubber is dried and placed back into the mother mold.
HINT: Do not leave the rubber in a heap. Instead let the mother mold do what she is supposed to do, cradle and hold the rubber. Rubber can have a “memory”, and leaving the rubber tossed about outside the mother mold may distort its shape and cause it not to fit back into the mother mold securely.
I would suggest that anyone who is wanting to learn to make molds for his or her own bronze casting, watch the process being done under a master mold maker. Contact a local foundry or artist and ask them if you can intern or apprentice under them to learn this process. They will most likely appreciate your eagerness and the help, especially if you can do it in their time frame. Remember they are on a deadline.
I might also suggest you take your education a bit further and ask the foundry if they will teach you to pour and pull your rubber molds. There is no better education in knowing if you created the mold properly than experiencing how the mold pulls from a wax. Though the process of creating a mold for bronze casting can feel daunting, with a little practice it is possible to begin to create your own molds, and in turn, save yourself a great deal of money in the process of bronze casting.
Writing An Article About This
I’m writing an article about this subject right now. I thought I would post this video to explain the topic. VIDEO NO LONGER AVAILABLE
It is about something called the Orphan Works Bill. This bill is not supported by most artists and will really be detrimental to our lively hood. I can hardly believe that it is being considered. If anyone reads this and would like to help please e-mailyour senator and tell the you do not support the Bill S.2913
Mold Making And Bronze Casting- Part 1
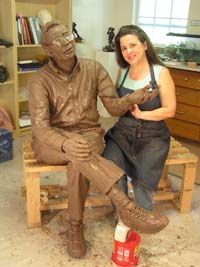
Created for Best of Artists and Artisans web site By Bridgette Mongeon © 2008
There is one question that I receive on a regular basis, “How do you make a mold for bronze casting, or how can I make my clay artwork into bronze?”
Though the process is quite detailed, I have recently made this video of the Dick Hathaway mold and bronze casting. It is not instructional but it does show the process. Watch the video and I’ll share some hints, and tips as well as some of my resources for materials that I use. Mold making and bronze casting is much too much to cover in one article, so check back next month for part two.
I have been making molds for years; however, I still find myself saying, “I could have done this one better.” I learn from each process. Attempting to make your first mold will feel overwhelming, but start with something simple. The one thing I have found that keeps me from beginning a project is not just the learning process, but also the daunting task of finding all the materials and tools I need. So for this months article I thought I would give you a list of my tools and materials used in the mold process, some of which you will see in the video If you proceed with a mold and need any further assistance or have any questions just go to my forum on my website, https://creativesculpture.com/forum and post your question. I’d prefer to answer your question on a forum. Then others might find our conversation at a later date and gain some knowledge. I’ll list the contact information of my suppliers at the end of this article, though I do encourage you to research suppliers in your own area.

TOOLS
When I am claying up seams, I heat the clay up in a microwave, bang it out into thick slabs with a rubber mallet, and then put it on the sculpture while it is warm. Often I search around the studio for jars, cans, and other items to hold up this seam. Pressing hot Klean Klay against the base of a jar will help to hold it in place, and the jar helps hold up the seam. If I need to clean up a seam, I’ll use my favorite dental tool. I use a round ribbon tool to carve the groove in the Klean Klay. This creates the “key” to keep the two pieces of rubber together. Kitchen knives come in handy to cut the clay to make a clean edge.

As you can tell, making the seams and preparing each piece can take a lot of time. It probably took me three days to cut and prepare the entire sculpture.
Don’t forget to leave an area to pour your wax into the mold. This can be the cut area. For example, where the arm was cut. Sometimes I create a clay spout, adding it to the cut areas to give me a good pour. If you look at the lower torso in the video, I put rubber over the entire cut section, between waist and lower torso, and poured the wax into the rear area.
I love power tools. It is a reciprocating saw that I use for cutting apart the sculpture. Using this tool is something I learned from the foundry.
The metal shims used in creating the seams on the upper torso and head are from Wholesale Tool and they are taped together with scotch tape. I have also seen other sculptors use plastic for shims. One of my cans of shims says the size is .0005. The shims should be thin enough so as not to make too big a gap when the rubber pieces are put together and not too thin so that it bends when you push it into the clay.
HINT
Be careful when using metal shims. Throughout the process, the shims disappear after being covered with rubber and plaster, you may have an edge stick out that can slice your hand.
MOLD RELEASE
Each sculpture piece is sprayed with a couple of coats of mold release agent. I never seem to have enough of this around. Be sure to keep a few cans on hand. Universal Mold Release costs about $11.30 a can and is purchased from Reynolds.
RUBBER
RUBBER
I have tried several different rubbers, but right now I am using Reynolds Rubber Brush- On 40, gallon kit. It costs around $120.00. It took about four of these to do the Dick Hathaway sculpture, a big investment. Remember though, a foundry would charge you about $7,000 to make a mold this size. I’m open to investigating less expensive rubbers, but dependability and longevity of a rubber is something to consider when comparing rubbers and I know this rubber fits that bill.
RUBBER Mold making is messy. I put paper, plastic, or cardboard around the mixing area. Save all of your large plastic yogurt and sour cream containers. These can be used over and over again for mixing rubber. This entire process is not very earth friendly and reusing containers helps ease my conscience a bit.
Mixing sticks. I use a lot of these, so I try to pick them up from the hardware store whenever I go. Usually they give them when you buy paint. I also look for anyone throwing away old shutters or shutter doors. The slats work perfectly for stirring sticks. Yes, the word is out, I garbage pick.
HINT
Be sure to keep the catalyst (yellow container) of your rubber covered while working with it, it can go bad.
HINT
Keep a stick to scoop out Part A and a separate stick for Part B and then another clean mixing stick. You don’t want to get any of part A into part B until you are ready to mix. You will notice in the video that I save my containers from sushi to set the cups in so they don’t drip all over the work area.
HINT
You must have equal parts. You must also be sure to mix thoroughly. If you are using yogurt containers be careful of the groves in the bottom of the container. You will want to be sure to mix every bit of it from the bottom. If you falter on these two hints, you will lose your mold and maybe your original.
GLOVES
Have plenty of gloves on hand. Mold making is very wasteful, but working without rubber gloves is maddening. I usually try to keep both vinyl and latex, just in case an apprentice prefers one to the other.
PAINT BRUSHES
You will use quite a few paintbrushes. I change out paintbrushes after each coat of rubber. One inch chip brushes work best for me, and I get mine from Montalbano Lumber, $14.04 a box Even though this is a little item, I suggest looking around for a good price per piece on these. You will use a lot.
HINT
When applying the first coat of rubber, be sure to dab the rubber into all crevices. The second and third coat will go much faster than the first. I like to have several pieces to work on to keep the flow going. That way I am not waiting around a long time for something to cure for the next coat. If you touch the rubber and it feels sticky but kind of leaves a fingerprint, it is ready for the next coat.
UNDERCUT PREPARATION
This is a step that is not covered in the video. The video does not show how to make sure a mother mold will come off of the rubber. It is a vital step. Please contact me and I’ll explain this or I’ll be sure to video tape it in detail the next time I make a mold.
NEXT MONTH – Making the mother mold
SUPPLIES AND SUPPLIERS
Paper or plastic to cover floor
Recipricating saw
Klean Klay
Rubber
Mold Release
Stiring Sticks
Yogurt Containers
Gloves
Microwave
Rubber mallet and tools to clean up seams
Large garbage can for disposing of gloves and brushes
Paper towels
Ceramic Store Tools and water base clay
1002 West 11th St.
Houston TX 77008
1-800 290-8990
http://www.ceramicstoreinc.com/
Circle Supply in Houston Hydrastone
6401 Long Point Rd # 506
Houston, TX 77055
(713) 688-9803
http://circle-supply.com/
Fine Art Foundry of Texas wax and bronze casting
6107 W34th
Houston, TX 77092
713-686-5567
http://www.fineartsfoundrytexas.com/
Klean Klay Clay for claying up the seams
P.O. Box 678
1019 Salamonie Ave.
Huntington, IN 46750
260-356-2328
http://www.kleanklay.com/
Montalbano Lumber Chip brushes
5850 N Shepherd Dr
Houston, TX 77091
Phone: 713-691-6611
http://www.montalbanolumber.com/
Reynolds Advanced Material Rubber, clay, mold release
5 locations 1-800-421-4378
http://www.reynoldsam.com/
Wholesale Tool Shims
Several locations
1-800-521-3420
http://www.wttool.com/
A Living Sculpture
This is my continuous work in progress. A living sculpture, a retreat and my commute to work. As I stated before this pond, stream and waterfall is something we have been working on for 10 years. This past week we finally finished it! O.k. there is still some things I would like to do.
First picture looks from the porch of our house to the small shed left, and the corner of the studio steps. When ever I come home from work ( 40′ commute) I take the long way!
Here is the view that clients see when they enter the backyard. The sculpture studio is downstairs and that is my office window in the loft. I can see the pond from my office. The stream runs along the walkway, as you walk to the studio. Tilly the turtle and her baby climb this stream and waterfall daily!
My husband hates the purple chairs, but I wanted to bring some color to this back yard and purple was my color of choice!
Tilly and her baby have come down to the lower pond after construction. I think they approve. Here Tilly is coming out of the pond ( lower right corner) There is rock that is supposed to stick out of the pond, but we had a lot of rain. Guess I’ll put my wet suit on and get back in to lift it up!
Stepping out of the office window onto the roof is the only way to get a picture like this. You can see a bit up the stream. The bench and chair in the middle of the yard is where my husband and I have our meetings, though I have to say we did take our shoes off and stick our feet in the pond the other day. We both thought that was a perfect meeting spot as well.

( you can see that about the middle of this picture is some liner. Here is the unfinished spot. A small beach is going here, for birds, easy out for Tilly, watering hole for dogs etc.)
It is my oasis, you could hardly tell that you are in the middle of the big city of Houston. Only downfall to this is getting a life size sculpture or bronze back and forth from the front, but we have done it and have tried to keep that in mind when putting together the walkways.
Certainly a living sculpture.
Was It An Angel In The Nativity Or A Dragon Fly?
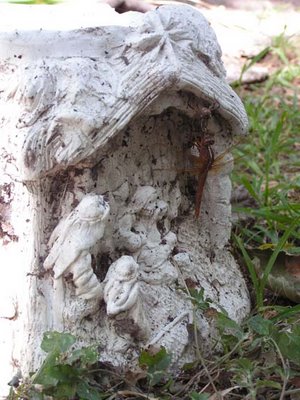
Here is a little pond biology. Dragon fly nymphs climb from our pond onto stalks and then hang there. Soon the dragon fly burst forth and hangs to dry. Once dry, they fly away to come back later and mate with another dragon fly or lay eggs. They are one of my favorite things about the pond. While getting ready to work on the pond this garden container that I created called “nativity” was sitting by the pond. I think I used it to weight down something during the winter. I looked closely and just about the place that an angel would be hanging there was this dragon fly. I thought it was so cool, I just had to share it.