Technology
Private Gathering on Art and Technology

shared information about incorporating
3D technology in the traditional sculpture
studio at Shidoni Foundry. The lecture
culminated with a viewing of the cast
sculpture and a foundry pour.
As many of you know, I am in New Mexico approving the sculpture of the 14+ foot bronze tiger that I created for Grambling State University in Louisiana. It is being cast by Shidoni Foundry. I also gave a presentation at Shidoni Foundry titled Taming the Beast: A Lecture on Fine Art, Craft and Technology. The lecture is about the process of creating the tiger, but also about some of the items in the new book that I am writing titled 3D Technology in Fine Art and Craft.
My very gracious hostess here in Santa Fe, Mary Anne Stickler has offered to have private gathering in her home for some of her friends who are interested in art, and great conversation. I’m so honored.
Date: Monday, November 18th
Time: 4:00 p.m.
If you miss either one of these lectures and gatherings, don’t fret. I’ll be back this spring doing something similar in Albuquerque-details to come. Oh, and if you want me to come and speak in your area, just give me a call.
_____________________________________________

Bridgette Mongeon is a sculptor, writer, illustrator and educator as well as a public speaker.
Her blog can be found at https://creativesculpture.com.
She is the vice chair of the planning committee for 3DCAMP Houston 2012 and 2013 http://www.3dcamphouston.com
Follow the artists on twitter twitter.com/Sculptorwriter
Taming The Beast: A Lecture On Fine Art, Craft And Technology

Taming the Beast: A Lecture on Fine Art, Craft and Technology
Sculptor Bridgette Mongeon will be presenting a lecture on incorporating digital technology in traditional art and craft on Saturday, November 16, 2013 at 10:00 at Shidoni Foundry, 1508 Bishops Lodge Road, Tesuque, NM 87574.
Digital Sculpting, CNC milling, and 3D printing, combined with traditional sculpture, is the way that Bridgette tamed the 15’ tiger that she sculpted for Grambling State University. Shidoni Foundry in Santa Fe, NM is casting the beast!
Bridgette will be discussing the technology, her process and how others are combining the technology in art, craft and science. The creative event will culminate with a viewing of the completed bronze tiger and a demonstration of a Shidoni bronze pour. Space is limited. To reserve space for Taming the Beast contact Shidoni Foundry office, 505-988-8001 ex 114
About the Artist
Houston, Texas sculptor, Bridgette Mongeon, is a traditional figurative sculptor of over 30 years. Bridgette began to incorporate digital technology in her work in 2008 and coauthored the book Digital Sculpting with Mudbox: Essential Tools and Techniques for Artists. Writing and lecturing about; art, marketing in the arts, creativity, and digital technology, gives her great pleasure. Bridgette holds a BA from Vermont College and an MFA from Goddard. She is presently working on a new book about 3D technology in art and craft.
_____________________________________________

Bridgette Mongeon is a sculptor, writer, illustrator and educator as well as a public speaker.
Her blog can be found at https://creativesculpture.com.
She is the vice chair of the planning committee for 3DCAMP Houston 2012 and 2013 http://www.3dcamphouston.com
Follow the artists on twitter twitter.com/Sculptorwriter
3D Technology in Art and Craft – A Question- 3D Printing in Color
I’m working on a new book that details 3D technology in Art and Craft. It will describe how to create art using such things as 3D printing, 3D scanning, 3D sculpting and 3D milling. It will show how to combine these technologies with traditional art and craft. It will also contain interviews with businesses and artists to discuss their processes. Finally it will be a one stop book that features vendors and other resources.
I’m culling through my many years of research and writing on this topic. I studied 3D technology as it is combined with art as my MFA, and have written and lectured on this topic often. I’m also looking at the new technology that is coming out. In light of that, I thought I would post some of my own questions on the topic. If you have an answer to these questions please feel free to post in the comments section of the blog or drop me a line. Please cite your answers when possible. I greatly appreciate it.
3D Question- printing in color.
I’m intrigued with printing in color.
As part of the book I really want to walk the reader through creating a piece of art that uses 3D scanning and 3D printing as the art interacts with natural surroundings. I wrote about that in a previous post. I love the video created by Greg Petchovsky who takes objects in the real world and then recreates them or adds to them in a 3D program and then prints them out using a 3Dprinter. I contacted Greg about this project, asked him how he scanned the color and what other details he could tell me about the quick projects in the video. He was kind enough to answer some questions. Here are his comments from the e mail
had my prints done by Shapeways, they used ZCorp 3d printers.
The material isn’t waterproof, it will warp and develop white discoloration if exposed to water. I haven’t left 3d prints outside for a long period of time, so I’m unsure how long they would hold up.
I set up the scale in 3ds Max. I just used calipers to measure the object, but in future I’m thinking I’d include a wooden ruler in the scan.
I don’t think I’d use masks or visibility to make meshes fit into each other. I’d try to use booleans. I haven’t experimented all that much with booleans in zbrush, but basically there’s a button over each subtool that lets you chose between additive, subtractive, or intersection. And the resulting mesh can be calculated using the “remesh all” button… though the results might be somewhat mushy. I believe similar (possibly better?) results can be achieved with dynamesh? And I guess the details could be re applied using projection.”
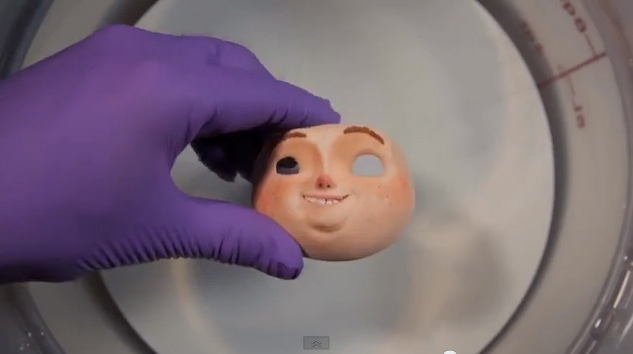
I am also intrigued with the work of Laika and how the puppeteers created the pieces for the making of the movie Paranorman. Each puppet was created using different expressions. These expressions were used with stop animation and some computer graphic work to create the film Paranorman. I’m assuming the super glue will help to strengthen the piece as well as keep it clean.
It is reported by the University of Texas at Austin Architecture school, in this article that using super glue can double the price of a 3D printed piece. I’m still not certain what the process is of “dipping” a piece in super glue/acetone. Seems like it would make a mess and be very difficult to handle. I can’t believe no one has figure out another way to harden these materials. Also, it looks like none of these things printed in color can be used outdoors, so I may have to modify my example for the book to use drift wood instead.
I contacted one of my go -to people on 3D printing Paul Cesak, who just happens to also be the guy that started the 3D printing group on linkedin. The 3D printing group is growing by leaps and bounds. He replies “only with 3D Systems can a 3D print have the full spectrum of color. The downside of that is that it is printed on plaster, is very fragile, and has the texture of sand. Indeed small details are either not printed or are lost in the post-processing.”
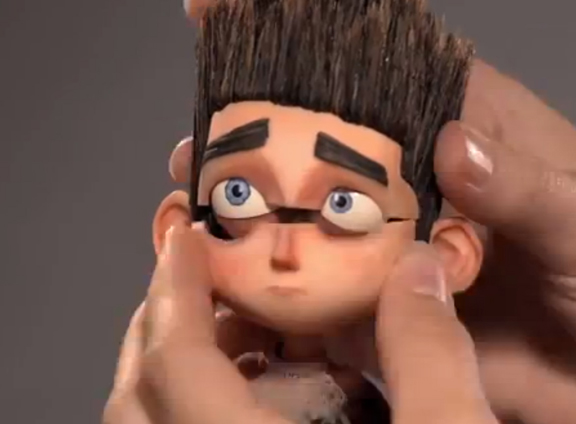
I contacted one of my go -to people on 3D printing Paul Cesak, who just happens to also be the guy that started the 3D printing group on linkedin. The 3D printing group is growing by leaps and bounds. He replies “only with 3D Systems can a 3D print have the full spectrum of color. The downside of that is that it is printed on plaster, is very fragile, and has the texture of sand. Indeed small details are either not printed or are lost in the post-processing.”
Another artist that I will be interviewing for the book is Eric Van Straaten. This video shows his work being created. I’m not sure he uses anything to strengthen his pieces. I’ll let you know after we talk for the book.
I have many questions.
QUESTION: how does an STL translate color? I though STL files did not have color?
QUESTION: What 3D printers can print in color?
QUESTION: If this is done through SLS printing, how does the laser depict color? ( I’m wondering if this can be explained simply)
QUESTION: is there nothing else that can strengthen the pieces using this type of 3D printing?
_____________________________________________

Bridgette Mongeon is a sculptor, writer, illustrator and educator as well as a public speaker.
Her blog can be found at https://creativesculpture.com.
She is the vice chair of the planning committee for 3DCAMP Houston 2012 and 2013 http://www.3dcamphouston.com
Follow the artists on twitter twitter.com/Sculptorwriter
Come And Put Your Head In The Mouth of A Tiger
My work has been accepted into the 3DCAMP Art Show! Well not all of it just the head!
I have just discovered that my tiger will be at the 3DCAMP event scheduled for October 5th. WHAT? Well not the entire 15 foot tiger, but the head. I’ll also have information that demonstrates the 3D process used in making this. You really should come by and see it, and have a picture taken with it.
No baby sacrifice is required, just sign up for a day of fun and brain stimulation at U of H. Here is the website. Oh, and tickets are limited so sign up today. And when you interact with this thing please send me some photographs so I can post them here!
If you would like to see the entire tiger visit the Grambling University Tiger Project blog where I am documenting the entire process. Check out the beginning of the blog to see the digital creation and learn about the CNC milling used to enlarge this beast.
Bridgette Mongeon is a sculptor, writer, illustrator and educator as well as a public speaker.
Her blog can be found at https://creativesculpture.com.
She is the vice chair of the planning committee for 3DCAMP Houston 2012 http://www.3dcamphouston.com
She is also the owner and creator of the God’s Word Collectible Sculpture series http://www.godsword.net
Follow the artists on twitter twitter.com/Sculptorwriter and twitter.com/creategodsword
Listen to The Creative Christian Podcast or the Inspiration/Generation Podcast
Click on Podcast Host Bios for a list of all podcasts.
Help With A Creative Adventure
As I posted in a previous post, I am writing a book Tra-digi-2014 Sculpture: Using 3d software, milling, scanning and printing in art and craft. In one section of the book I am interested in documenting how to scan things in nature and then create 3d objects in the computer that fit into nature. I suppose I was first introduced to this incredible concept by an online video that I found and played at 3DCAMP Houston 2012. The video created by Greg Petchovsky takes objects in the real world and then recreates them or adds to them in a 3D program and then prints them out using a 3Dprinter.
A rather industrious project that I am trying to do and to record for the book is to create a home in a hole in my tree. I have scanned the tree using 123D catch and would love to be able to get what I need from using just that program, as it is extremely easy to use and free. Free is good because it is not a stumbling block to the readers of the book. I do plan on scanning it with my Next Engine Scanner as well. It will be interesting to see exactly what I will need to complete this project.
I’m going to contact Greg and ask him some of my questions. I will also be looking for printing companies that can help me create this piece for the book, yes, I am happy to plug your company. I’ll include Greg’s video below as well as a short clip of my results from 123D Catch and ZBrush.
Like I need to make this job any harder, I also hope to create some interaction with the piece. That means that I want to hide sensors, lights … so that things that will happen when one walks by. Now to do this part I plan on contacting my resources at TX RX to help me figure out the electronics, and I’m sure that trying to hide these things in channels in the artwork will also pose a challenge.
I won’t be able to update my process on this project here, as I don’t want to spoil it for those wanting to read the book. If you should be able to help with any of my questions, suggestions or thoughts please contact me through my contact form on my website or through facebook.
Video by Greg Petchovsky
Video of my scan and ZBrush
Questions
How do you see the color when it is in Zbrush, as Greg has in the video?
Where did Greg have his printed, in what machine?
What is the stability of the color and what products can work outside?
Any secrets to how to get the size to match. I’m back to the idea that Zbrush really needs real sizes.
Zbrush- is there away to create an object that will fit in the hole of the tree, and perhpas use a mask and visibility to get rid of the areas that are not needed?

Bridgette Mongeon is a sculptor, writer, illustrator and educator as well as a public speaker.
Her blog can be found at https://creativesculpture.com.
She is the vice chair of the planning committee for 3DCAMP Houston 2012 http://www.3dcamphouston.com
She is also the owner and creator of the God’s Word Collectible Sculpture series http://www.godsword.net
Follow the artists on twitter twitter.com/Sculptorwriter and twitter.com/creategodsword
Listen to The Creative Christian Podcast or the Inspiration/Generation Podcast
Click on Podcast Host Bios for a list of all podcasts.
A New Book—A Resource Book For Those Creating Physical Objects Using 3D Technology!
I’m working on a new book
Tra-digi-2014 Sculpture:
Using 3d software, milling, scanning and printing in art and craft.
At least that is what the book is called at this moment.
A single source for incorporating 3D printing, 3D scanning and 3D milling into your art.
Tra-digi 2014—Sculpture: How to use 3D printing, milling and scanning in art and craft
- Do you want a 3D model of your child for your computer? Here is how to do it for free.
- Do you want to take a virtual sculpture and make it into a 3D print in clay, metal or even glass? Here are the steps, tools and resources to do just that.
- Have you thought of carving your ideas into wood, or stone but you can’t hold a hammer and mallet?
- Do you want to take a small sculpture made by hand and enlarge it to a monumental piece of art?
- Would you like to have a digital scan of your surroundings?
With the steps in Tra-digi 2014-Sculpture you can expand your medium as an artist, save yourself time in the traditional bronze casting and enlarging process. This give you more time to create!
But beware, there are some pitfalls, some hurtles and legalities associated with using traditional and digital processes. Learn how to protect yourself and your art as you create new masterpieces that could never be created before.
Bridgette Mongeon is a sculptor, writer, illustrator and educator as well as a public speaker.
Her blog can be found at https://creativesculpture.com.
She is the vice chair of the planning committee for 3DCAMP Houston 2012 http://www.3dcamphouston.com
She is also the owner and creator of the God’s Word Collectible Sculpture series http://www.godsword.net
Follow the artists on twitter twitter.com/Sculptorwriter and twitter.com/creategodsword
Listen to The Creative Christian Podcast or the Inspiration/Generation Podcast
Click on Podcast Host Bios for a list of all podcasts.
CNC Milling And CarveWright Conference

I could have done it without the use of CNC
milling. Oh yes, please note there is another
3 foot of rock that goes under this sculpture.
I have been compiling information and resources for a book that I am writing that talks about incorporating digital and traditional process in art. I call this marriage of the two -Tradigi art. I have been trying to educate others on the process of using 3D technology for a few years. Mike de la Flor and I wrote Digital Sculpting With Mudbox Essential Tools and Techniques and spent a chapter talking about 3D scanning, printing and milling. Our book, I believe, was one of the first that talks about how to get virtual pieces out of the computer and into a physical form. When I first started to do this, many CG people would ask, “Why do you want to get your designs out of the computer?” These are people who use the computer generated designs in movies, video, gaming etc. Without bringing virtual pieces into a physical world my designs are pretty much worthless to me.

created in the computer and the milled out foam
covered with a fine layer of clay.
Once the client approves the clay the sculpture
is taken into the lost wax method of bronze casting.
I am inspired to educate others on how to do these things and the possibilities of incorporating this type of work into their traditional studios. Here is a pdf of a 2008 article in Sculptural Review that I wrote about the process of CNC milling in art.
I have been using CNC milling of foam for a few years now. My two primary vendors are Synappsys in Oklahoma and Across the Board Creations in Canada. I have described some of my processes in a You tube video on the subject. I also have project blogs for the last several projects that talk about using the CNC milling of foam with my designs. I used CNC Milling on the Prairie View Panther, the Evelyn Rubenstein Sculpture for the Jewish Community Center and most recently on this enormous sculpture of the Tiger for Grambling State University.
I have also watched in fascination and excitement about the CNC Milling in Stone. All of these tools expand my tool set and save a sculptor’s hands from very damaging wear and tear.
Steven Ramirez of Smash Designs introduced me to the CarveWright . He was one of our speakers last year at 3DCAMP Houston. Once I saw the CarveWright and it’s possibilities I was very, very intrigued. I had been looking for a vendor that might mill my work. I’m still looking for this type of vendor. I had also been searching for others who had been using CNC milling in their artwork. I wanted to feature them in the book, and yes, I am entertaining getting a CarveWright of my own.
3DCAMP is a 3D symposium on everything 3D. It is hosted this year by the department of Architecture at the University of Houston. The date is October 5, 2013. The cost last year was only $15. and this year will be raised to $30 for professionals and $15 for students. A great prices for so much information and resources in one space. We had hoped that CarveWright might be a sponsor for last years 3DCAMP event, and would be able to discuss more about milling at 3DCAMP.

What is a CarveWright? It is an affordable consumer CNC milling machine that gives you the opportunity to design your own patterns, or use patterns provided with the machine and mill them out in many different materials. When learning about the CarveWright Conference, I was intrigued, not only because of my desire to try this machine, but also because I really wanted to gather more information for the book.
I learned many things from attending the CarveWright conference and was intrigued by the many people that I met. Of course, I’m looking at this tool and thinking, how can I push it like no one has ever pushed it before. How can I sculpt using this tool? I’m not the only one thinking about pushing the boundaries as Joe Lovchik, one of the owners of CarveWright was displaying how to use the tool to not only carve wood, but carve other things like foam, plastic and even wax. He showed how he used the CarveWright to make a pattern for pouring concrete, stamping leather, creating incredible lithophanes. The possibilities really made your head spin.

Besides learning the software that comes with the program, some of which I hear is some of the best for CNC milling, we heard what others were doing with the CarveWright. Michael Tyler displayed some of his creations and talked about inspiration. I loved learning about the stains and patinas he is using called Sculpture Nouveau. They are breathtaking! Joe Ragsdale talked about carving photos in wood. The feature that I think would be easily applicable to my own studio process is the carving of letters. I often get asked to incorporate type into my sculptures. This is not an easy task and takes a great deal of handwork. For example, the newspaper that the newsboy holds has copy that is individualized for each client that purchases this bronze. I have to change out the headline and subhead so that it is pertinent to those who are purchasing this bronze. You can be sure that the next time this happens I’ll be scanning this newspaper and carving it with a CarveWright. Oh, yes, I failed to mention, the CarveWright has a point scanner that you can purchase as well.
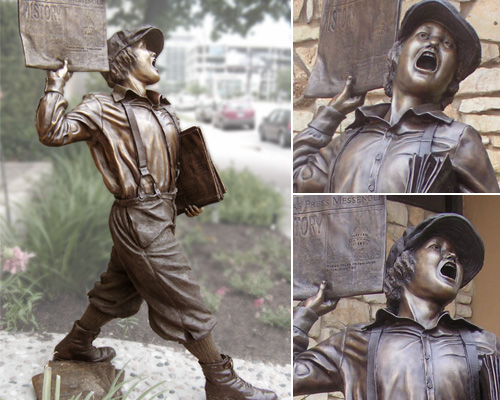
The possibilities and relationship between me and CNC and me and CarveWright are just beginning. I hope they will help me to push the limits of their product with my designs and look forward to working with them on this. I can’t wait to see what I come up with for the book. My head is already thinking in that strange 3D way. Thanks CarveWright for the information and the inspiration.
_______________________________________________
Bridgette Mongeon is a sculptor, writer, illustrator and educator as well as a public speaker.
Her blog can be found at https://creativesculpture.com.
She is the vice chair of the planning committee for 3DCAMP Houston 2012 http://www.3dcamphouston.com
She is also the owner and creator of the God’s Word Collectible Sculpture series http://www.godsword.net
Follow the artists on twitter twitter.com/Sculptorwriter and twitter.com/creategodsword
Listen to The Creative Christian Podcast or the Inspiration/Generation Podcast
Click on Podcast Host Bios for a list of all podcasts.
Measuring Tape in ZBrush

Recently I posted about my need for a measuring tape in ZBrush,. I created an entire post about my need. I have to say, this is not my first time requesting this from ZBrush, but it is the first time that someone replied and said, “hey, they finally gave us one and this is how you use it.” Apparently the transpose line can be made into a measuring tape. The transpose line is the line that comes up when you are trying to move, scale or rotate an object. To create the calibrations of the transpose line find “preferences” in your menu and scroll down to “transpose line” and then indicate your units of measurements.

Thanks to the guys on the Pixologic forum for sharing as well as the ZBrush, group on Facebook. I get all of my answers from these guys.
Thanks also to Pixologic for hearing my request for all of these years. I do find that I actually still have to count the units as I’m working. Don’t make the mistake like I did, If you want 13 feet you need 15 tick marks. I would suggest to set your measurements and then count the units to be sure it is correct. Missing a foot on my sculpture or even a 1/2 a foot would be tragic.
It would be great if all of the measurements actually appeared in a box when you used the transpose line. For example, after using the transpose line I could look ,and see if what I have drawn is actually the amount of feet I need? In the case of the tiger I have decided to sculpt him in two parts and I need to be sure those two parts will fit in the 9 foot clearing of the studio. I’m working through this, and ZBrush, is helping considerably not only in figuring out the perfect division for the tigers parts, but also to know how big to make my base and and how that all fits together. Maybe these measurements appear somewhere that I don’t know about but my further request for Pixolboic would be if these measurements showed up and as I use the transpose tool I could check myself. IE… Ah yes, that is 15′ 3″ and the width then this is……
NOTE: the way I separated my tiger into two subtools
1. I made a mask over the area I wanted to divide ( control, click and drag)
2. I split those polygroups to make individual subtools here is how.
FYI HERE IS THE ANSWER?
Someone suggested I try these calipers. Why have I not heard about Screen Calipers from Ionico sooner? With all of my posts and rantings about a sculptor needing calipers you would have thought this would be brought to my attention sooner. I checked… they work on PC and Mac. Well, I’m going to contact the company to see if I can review these calibers and if they work post some tutorials about how I use them. I’ll let you know.
_______________________________________________
Bridgette Mongeon is a sculptor, writer, illustrator and educator as well as a public speaker.
Her blog can be found at https://creativesculpture.com.
She is the vice chair of the planning committee for 3DCAMP Houston 2012 http://www.3dcamphouston.com
She is also the owner and creator of the God’s Word Collectible Sculpture series http://www.godsword.net
Follow the artists on twitter twitter.com/Sculptorwriter and twitter.com/creategodsword
Listen to The Creative Christian Podcast or the Inspiration/Generation Podcast
Click on Podcast Host Bios for a list of all podcasts.
I Really Need A Measuring Tape in ZBrush or Mudbox
When I started in ZBrush and Mudbox years ago, the computer graphics world ( CG) would often say, “Why do you want to get things out of the computer?” I felt like I was just told I had purple spots on my face. I am a traditional sculptor who uses digital process to create sculpture in the physical form. I have a variety of things that I do that incorporate both traditional and digital or what I call tra-digi art. I know my use of these digital processes is not the way others use them, but it is how I make my living. Oh, and by the way, if you ever want to bring me in to lecture on this subject I would be happy to do so.
When I was at the ZBrush booth at SIGGRAPH last year I saw that someone mentioned that others were translating their designs into the real world. So, I’m not alone.
PIXOLOGIC>>>>GIVE ME A MEASURING TAPE.. PLEASE!
Over the years I have found one thing is a constant – I need a measuring tape! The hard part about this is that in the computer your sculpture is not really any size. It lives in a virtual world with virtual coordinates. However, to get this virtual sculpture to live in a real world I need to compare it to the real world. Over the years this problem has come up again and again.
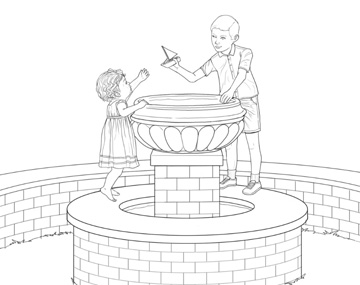
I would still need to create this digitally.
PRESENTATIONS- Comparison to what is there.
This usually happens when I’m working out the design, For example the landscape architect gives me blue prints and I need to come up with something. In the case of the fountain I could go and take pictures of what was created on the job site. The client wanted two children, and I was to incorporate the fountain base, and another piece that would sit on top. I would have loved to create this in ZBrush, but I opted for a simple sketch because of the limitations of measuring.

CAN I SHIP IT?
I know that someone working in the computer may not be thinking about shipping their final product. But I ship bronze sculptures all of the time. In many cases this is something I work out in the design process. If I can figure out how to modify the sculpture sometimes, it can save thousands of dollars. For example, I modified the design of the floor of the sculpture of the praying man to be able to fit the width of my van and still be life-size. I was able to do this in the sculpting process when in my traditional studio but there are other times I need this as well. Shipping the Tiger sculpture from my studio in Houston, Texas to Louisiana is a massive investment 7,000- 10,000. The tiger will have to ship on its side. However, I need to be sure that it can do so and fit on the flat bed trailer with packing.

MILLING?
Most of my sculptures, once created and revised in the computer are enlarged digitally in foam. This takes the place of doing the traditional armature of welding and pointing up as done in the past. Synappsys Digital Services does most of my enlarging. They figure out the mass if I give them the height, but it is often necessary to figure measurements out in the design. In
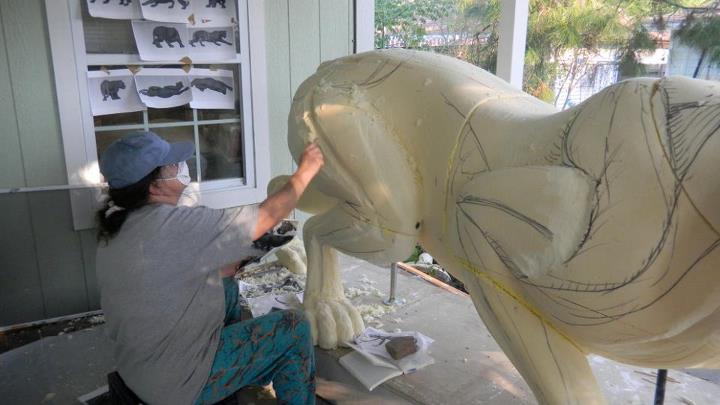
Often in the design stage it would help to be able to say, if it is this height,
what is the width at this place in the sculpture.
the case of the Tiger sculpture I lowered the head and the arm of the tiger, mostly because I could not find a warehouse big enough to allow me to sculpt that size piece. Subtracting a foot, by lowering the hand/head helped the design, but also give me a little more room to work. I would not have known to do that had I not measured in advance.
ARMATURE?
I’m taking time to write this post as I work diligently on trying to figure out the armature for the 13+ foot tiger. Though I can twirl the image around in my computer by pressing certain keys, in the real world this sculpture will have gravity and weight to deal with. The foam of the tiger, once togther will probably weight about 170 lbs. Then we add a layer of wax and a fine layer of clay. This will probably add about 400+ lbs to the tiger alone. Having the proper armature to hold this tiger up is imperative. Without it I could have the entire thing fall and, God forbid, be under it when it does. If I had a measuring tape in zbrush I could be making a schematic for my carpenter to build my base and armatures. I am also looking at a way to create the sculpture separately cutting the pieces in 1/2 so that I don’ t have to carve 15 feet in the air. Oh I wish I had a measuring tape.

Work around.
Yes there are probably ways to work around this. For example, I know the man in the scene if 6 feet, I can make a long flat piece that measures 6 feet and work with that. But being able to give one element a size, the man is 6 feet—and then able to click anywhere else on the sculpture to see what that size is in relation to the given size of the man- this would make my life a lot easier. So how about it Pixologic? Can I please have a measuring tape in the next version?
These are only a quick few ways I can see that having a measuring tape in a program like ZBrush or Mudbox would really help my work flow, and might even help to extend the buyers of these programs. In my speaking engagements I often tell my audience that I turned to the use of digital tools to extend my career. Pushing around clay with my hands has caused some great aches and pains over the years. Most of my audience wants to learn these processes as well, for just these reasons. Please give a listen Pixologic and Autodesk lets see how you measure up!
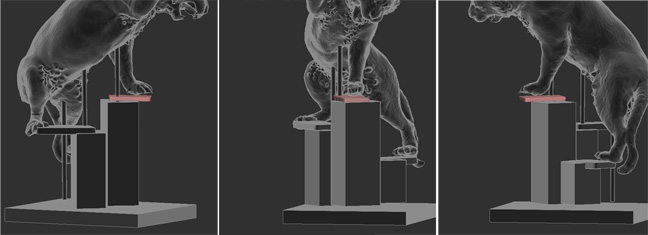
_______________________________________________

Bridgette Mongeon is a sculptor, writer, illustrator and educator as well as a public speaker.
Her blog can be found at https://creativesculpture.com.
She is the vice chair of the planning committee for 3DCAMP Houston 2012 http://www.3dcamphouston.com
She is also the owner and creator of the God’s Word Collectible Sculpture series http://www.godsword.net
Follow the artists on twitter twitter.com/Sculptorwriter and twitter.com/creategodsword
Listen to The Creative Christian Podcast or the Inspiration/Generation Podcast
Click on Podcast Host Bios for a list of all podcasts.
Figuring Challenges, Both Digitally and Traditionally
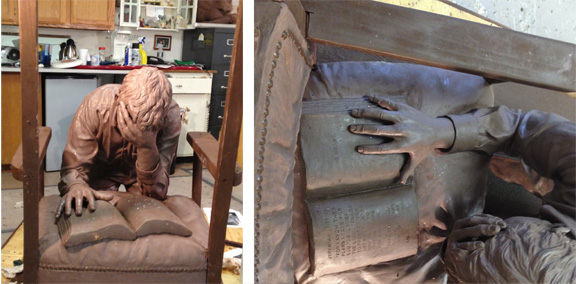
Here is the challenge
I’m trying to create quite a bit of text in a sculpture. Traditionally I prefer when text is created in a sculpture is is recessed as apposed to sticking out of the clay. Usually I create this type of affect with the following steps.
TRADITIONAL WAY
1. Set the text in a program on the computer. The kerning or the spacing between the letters must be a lot as you want the words to translate to the clay and not get cut apart in the steps that are to come up- the mold making, wax pouring and bronze casting.
2. Text also must be a good text for this process. Having small white space in the middle of a P is hard to keep through this process. I usually go with a Futura or Helvetica type face and make it bold. In this case all upper case will translate better through the process.
3. Print out the properly kerned text and then lay it over the clay. Very carefully scribe each letter into the clay. Then when the paper is lifted off you must carefully cut each letter with an exacto knife, holding the knife on an angel so you get the “chiseled” look and the mold will pull easily.
The difficulty with this traditional way, even though I have already paid an intern to scribe every letter, is that it is taking me about 1 hour per 3 lines and I don’t really like the way it looks. So I’m exploring digital processes.
WHAT THIS IS FOR?
This is for a life size bronze sculpture. The bible that sits on the seat and is already roughed in. The client wants text in the bible so a scripture will be read. It will set into the bible, not come out of it. I started hand carving it but it is not crisp enough and taking forever.
POSSIBILITIES?
I have in the past had rubber stamps made for a sculpture, but remember these are in reverse. A vendor suggested using this company in Houston. They have done a lot of work for my other vendor American Collectors Studio
Lobue’s Rubber stamps# is 713-652-0031 ,1228 McGowen at Caroline
I also own a variety of “press in letters” for clay. But when you press in letters the clay has to go somewhere and so you get this bumpy look. It also is a fine art to make all of your words line up and not be bouncing all over the place. And finally will they have a good type face at the right size that you need? That is the hardest part. I will try to list these press in type letters at a later date. Some sculptors might find it useful.
DIGITAL WAY
I know that there are 3d printed materials that are flexible like rubber. So I am looking for this to be printed as a flexible material. Crisp text. That way, I can cut away the top layer of this clay page and set this into the clay. Because the bible is created with a dip the flexible material will allow me to creatively put it on the bible with the wave that it needs. So I’m presently searching local vendors that can do this in Houston. I know that I could probably go to imaterialze or Shapeways, but they do this out of the country and I’m on a deadline.
Jose at the University of Houston 3d printing department made a suggestion- more on that later.
BUT WHAT ABOUT YOUR FILE?
We needed an stl file. That is what is used for 3d printing. I tired doing this simple project of insetting copy in zbrush and did not have much success. I was disappointed. I love the program but really wish some things were not so hard. My 3d super hero husband created outlines in illustrator and brought it into 3ds max using Boolean to extract the type. We estimated it to be 1/4 inch thick with a 1/8 inset. I know that the more material the print the bigger the cost. I’m waiting to see if I need to revise the files. More on this later. Lets see what company saves the day, with as little cost and quick turn around!
MORE TO COME!
and the winner is…. Loboue’s! they are charging $80 a page, certainly worth it. Having it set digitally was 500-1,000. Sometimes the old way is the best way.
Bridgette Mongeon created this sculpture for Dallas Baptist University. If you would like to read the entire process on the artists project blog for this project visit http://prayingmansculpture.blogspot.com/ .