Sculpture
Going High For Detail
Once the Grambling Tiger sculpture is sandblasted, I must check it out to be sure that there are not corrections. I walk around the sculpture or in this case, climb around the sculpture looking for places for them to fix. I mark them with a marker and then the foundry men work their magic. I have a very intimate relationship with this height and this tiger head.
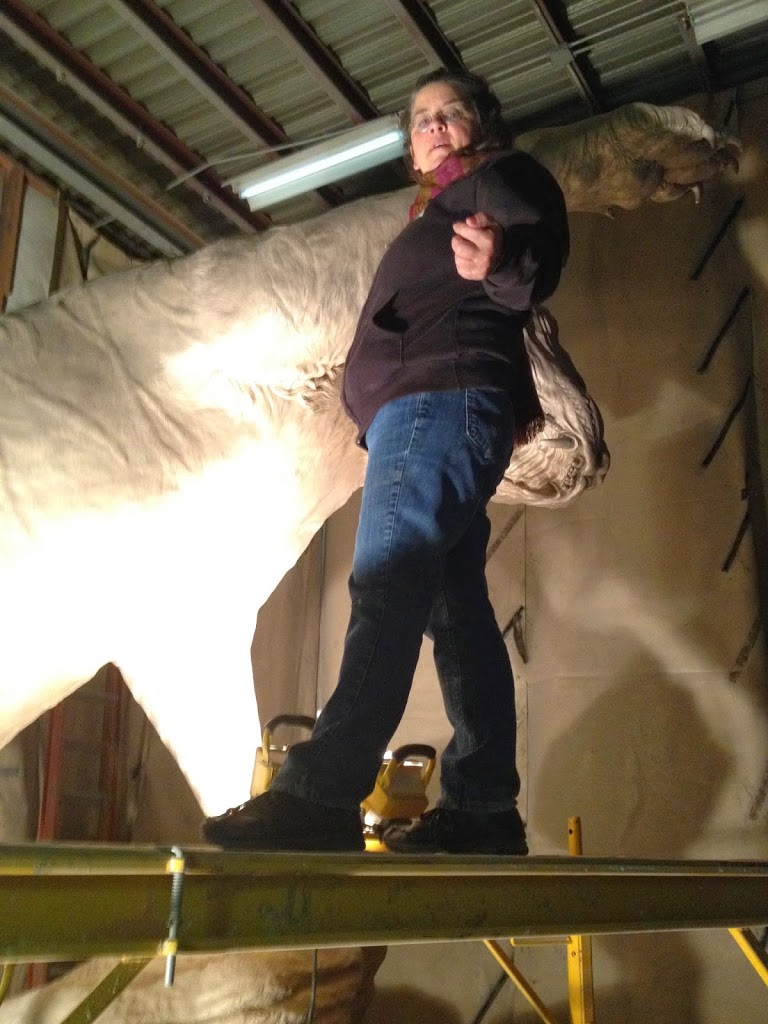
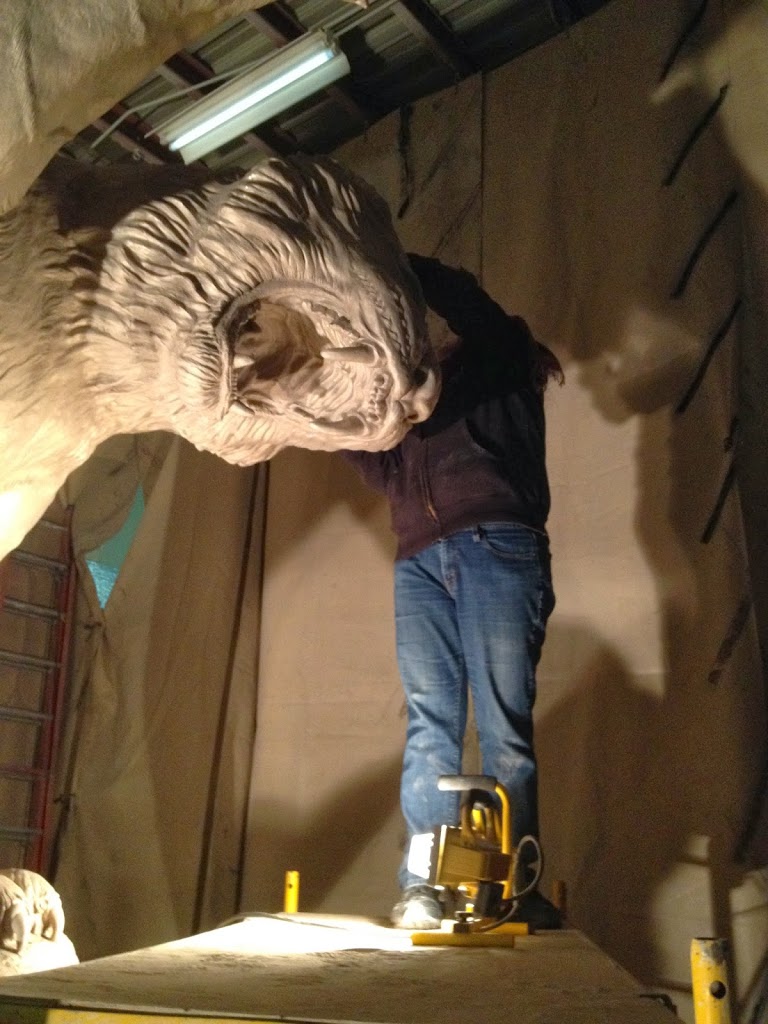
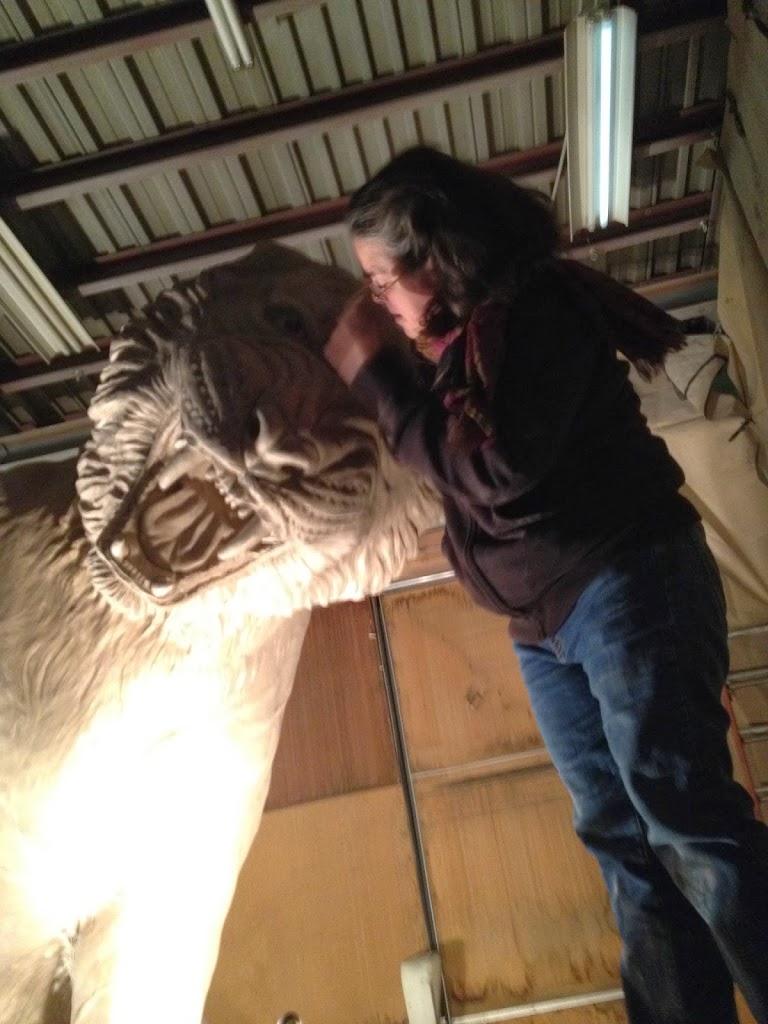
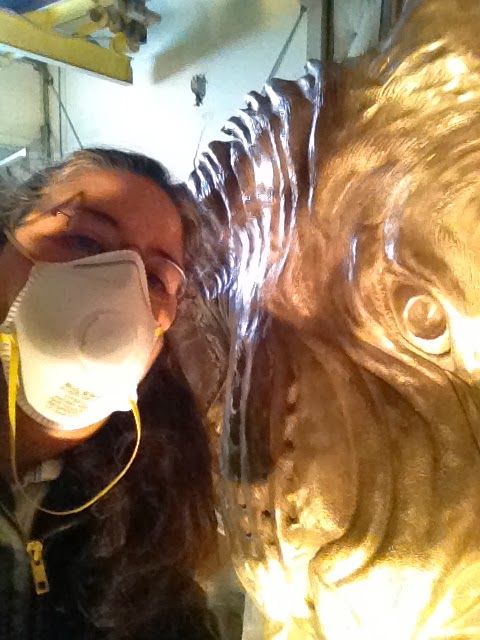
A Cat Finds His/Her Rock
The foundry works diligently to meet the deadline. Each of the many pieces of metal must be welded together seamlessly. Once the cat is almost finished, it is moved from one side of the foundry to the other.
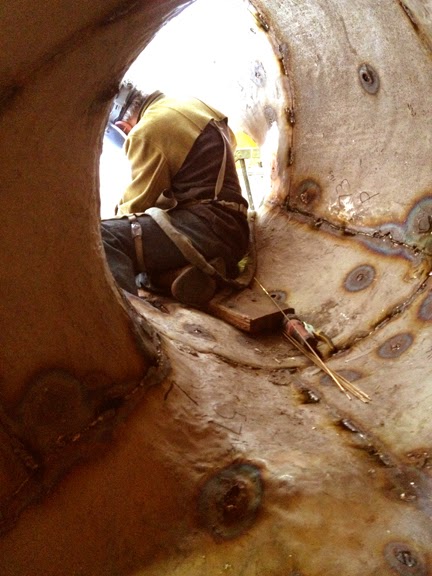
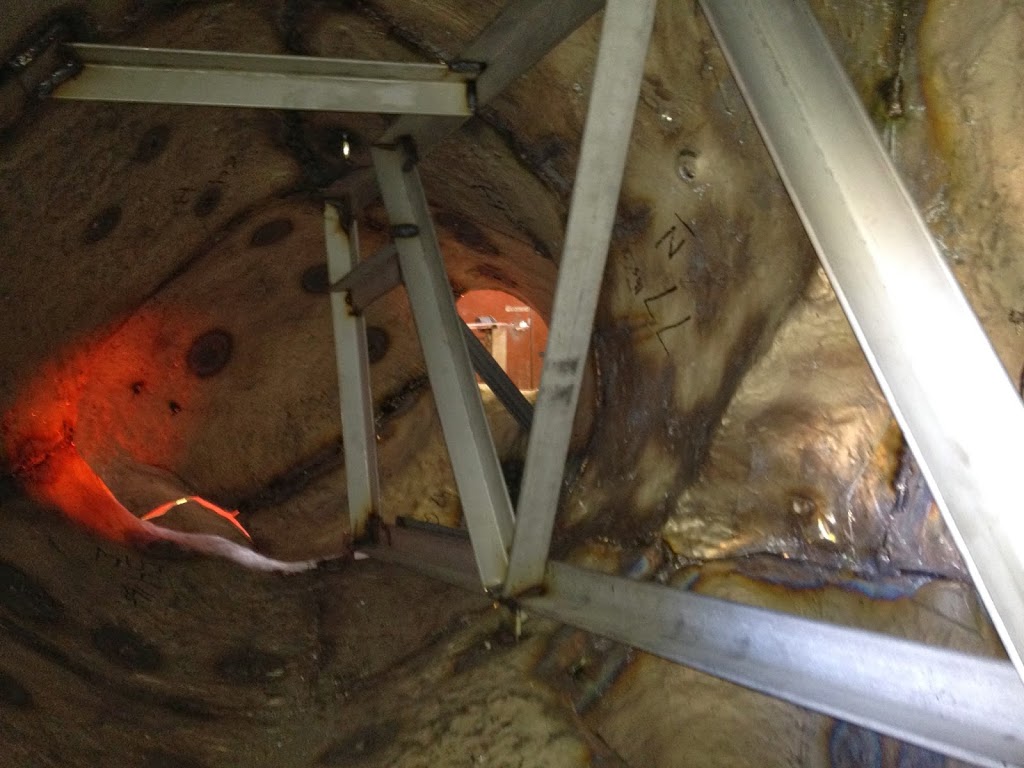
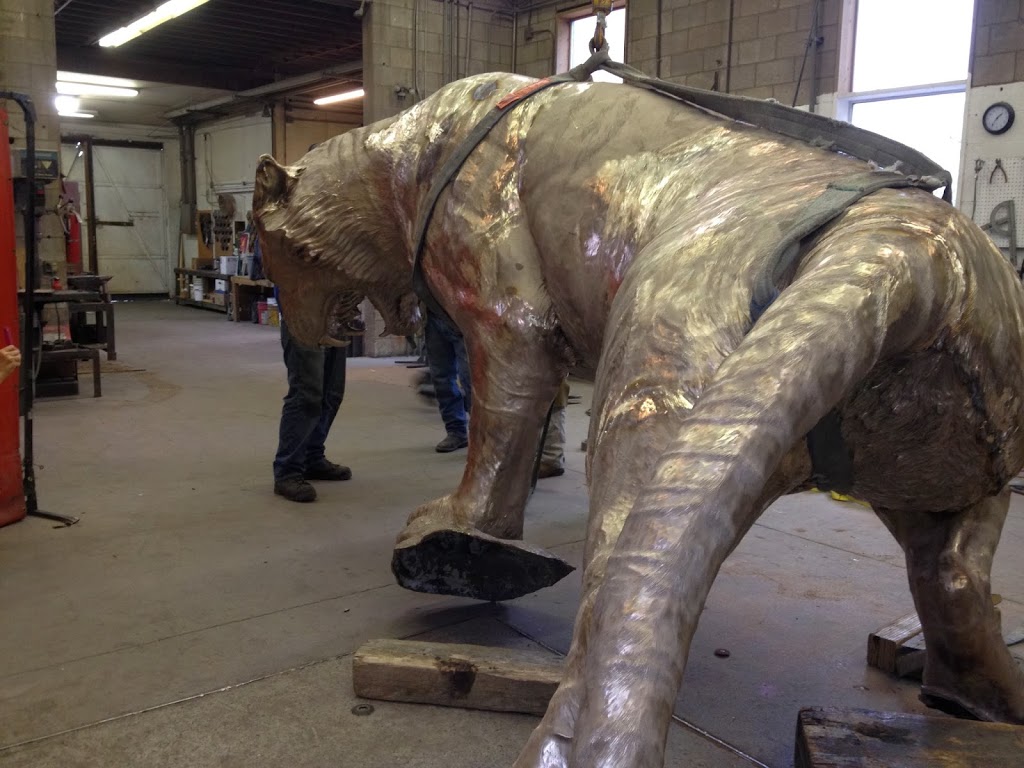
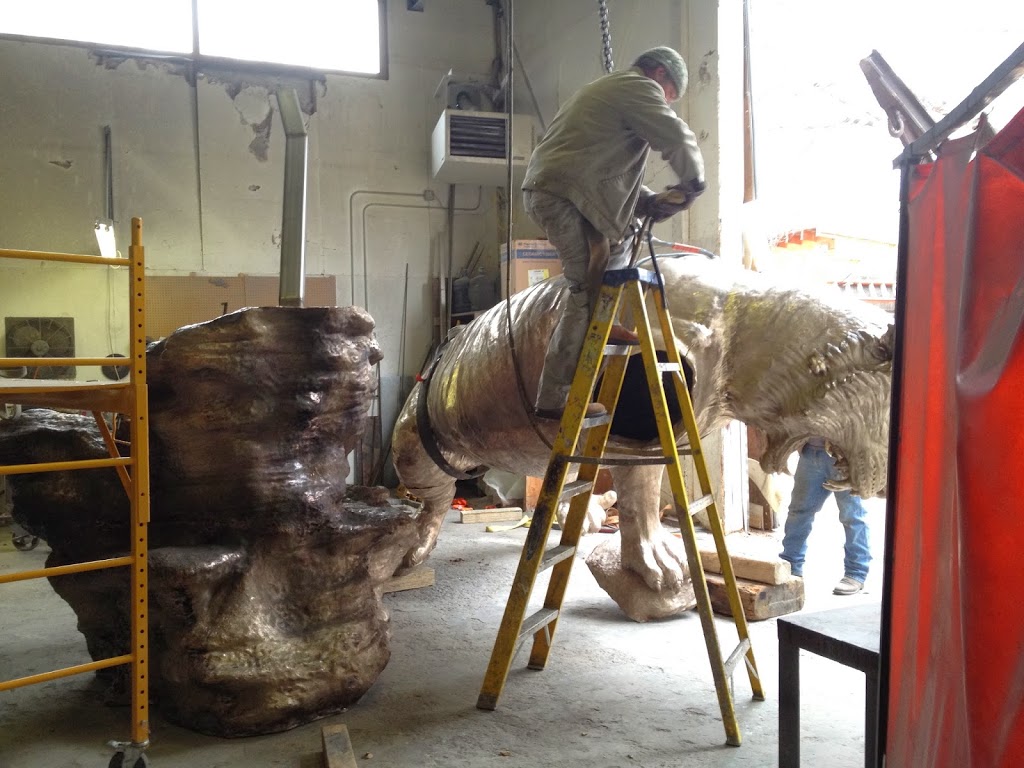
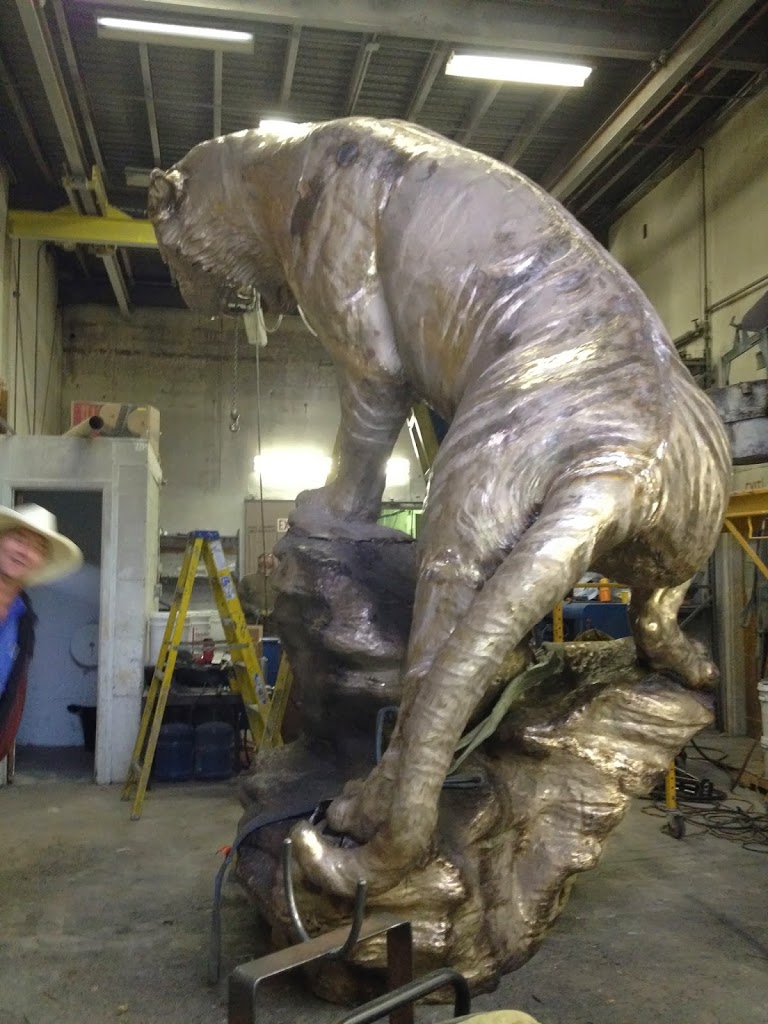
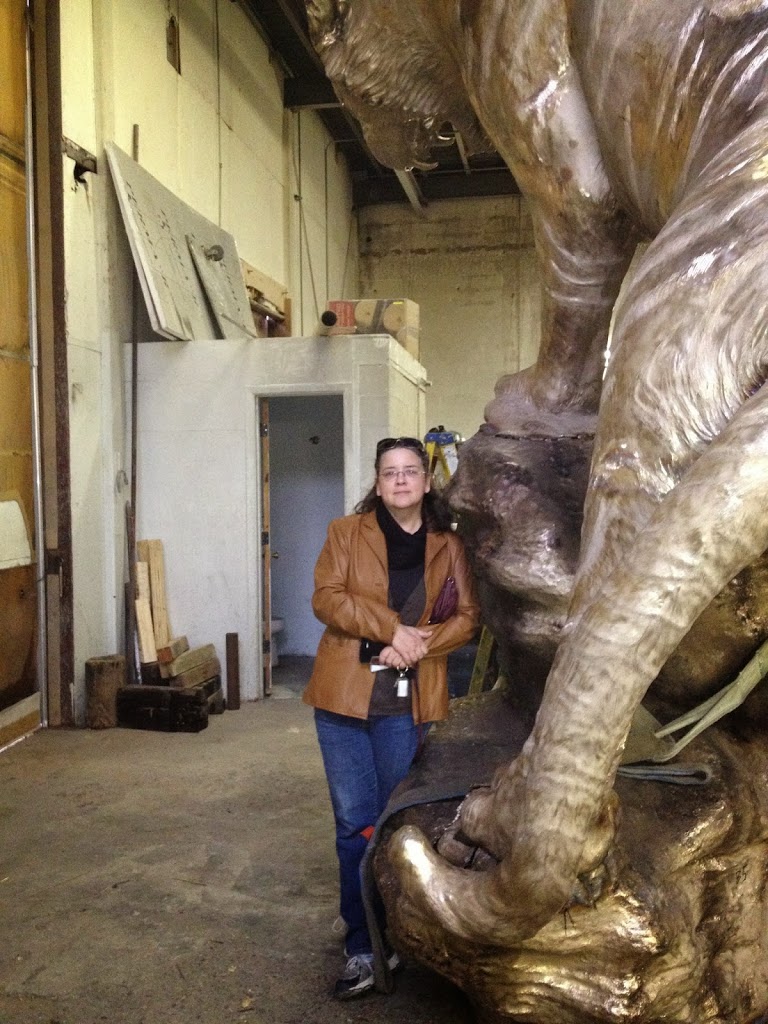
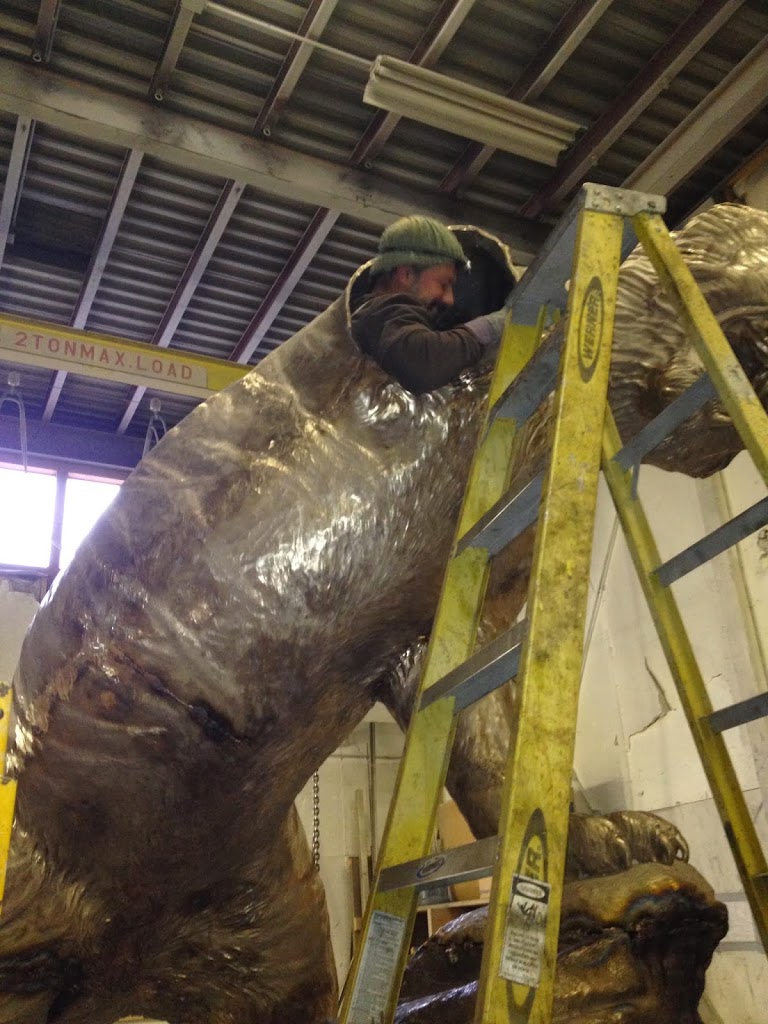
arm. It is a tight fit.
Wrestling The Tiger
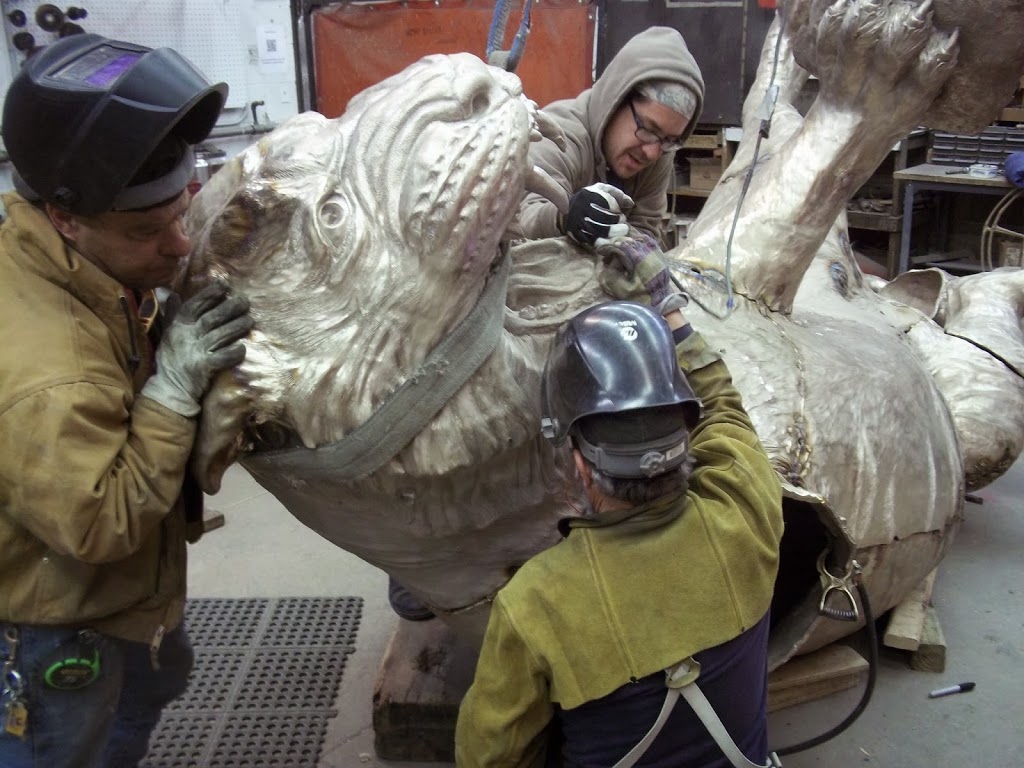
I’m headed to the foundry in New Mexico very soon to monitor the rest of the progress and to do the final coloring of the Grambling State tiger. Then we will load it up on the flat bed and watch for it to arrive on campus. Not sure how much posting I’ll be able to do while there. You will get glimmers of the sculpture in the snap shots that I take. Not until the great reveal will you be able to see the entire sculpture complete. Unless… you are in NM on November 16th. I’ll be giving a lecture on “Taming the beast” at Shidoni Foundry. The lecture will culminate with watching a bronze pour. (Not the tiger as it will be complete.) We will also be able to take a look at the finished tiger. I can hardly wait.
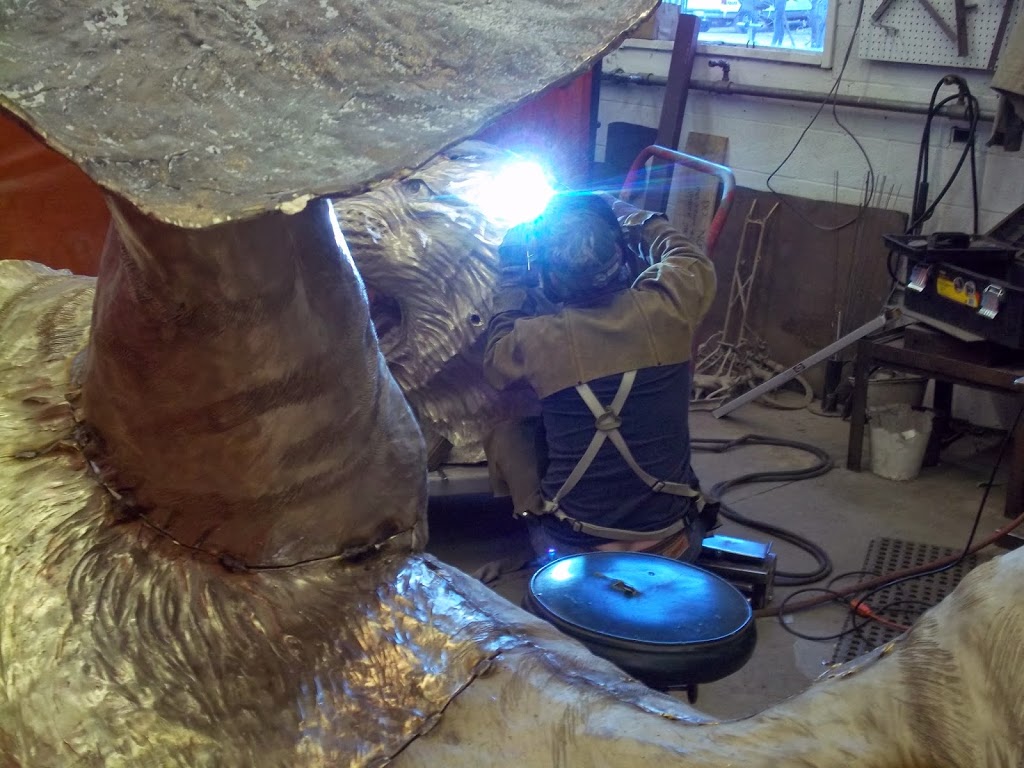

I’d be happy to repeat this lecture at Grambling for those who are interested. Looks like we are leaning toward delivery of the sculpture in the first week of December.
Rocking Out Again
The rocks in this Grambling State tiger sculpture are just as massive as the tiger itself. The many, many pieces of the sculpture are being welded together. The foundry will match my sculpted textures. It is a huge puzzle to figure out where everything goes. There will also be an internal structure inside the sculpture to give it support.
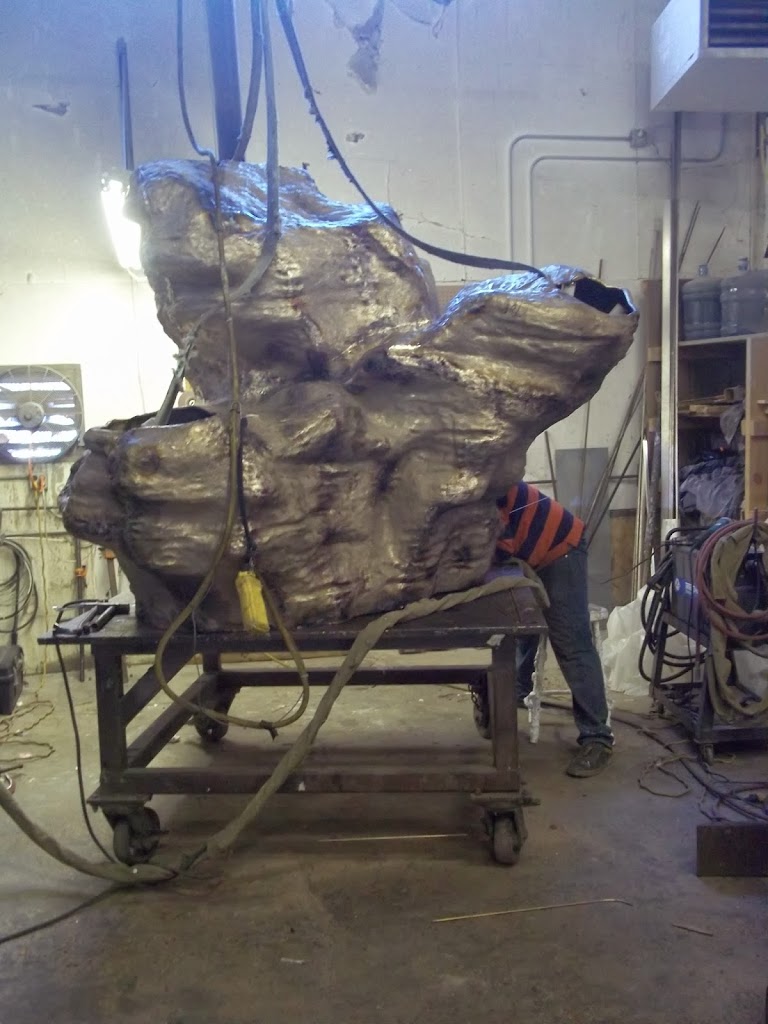
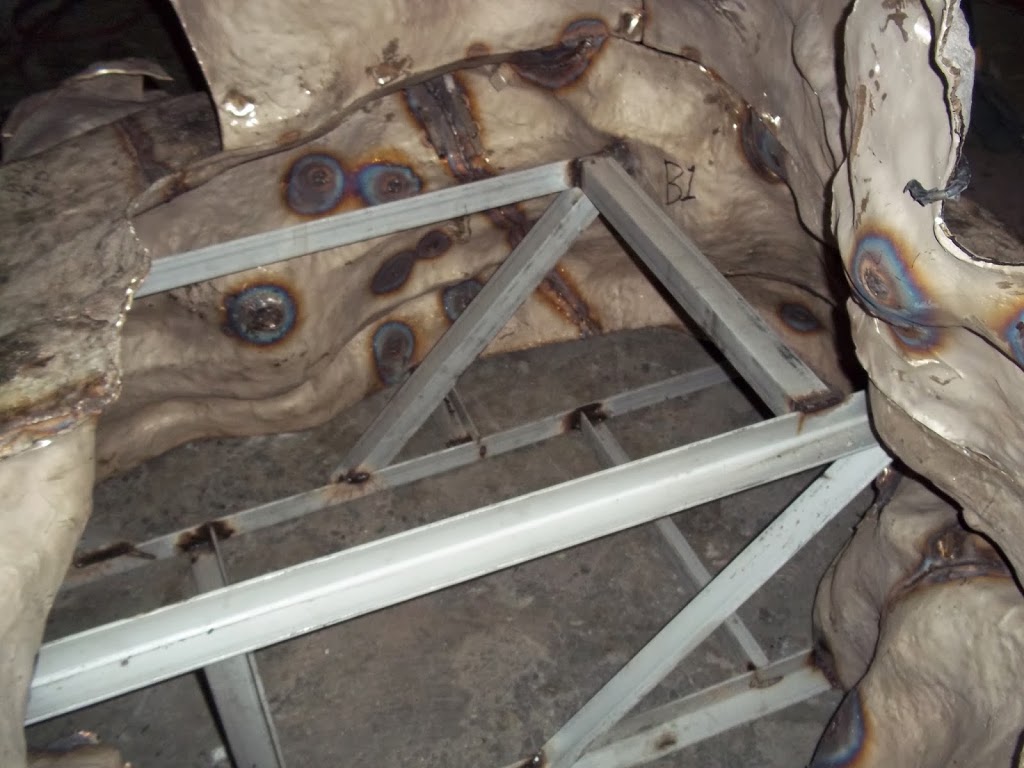

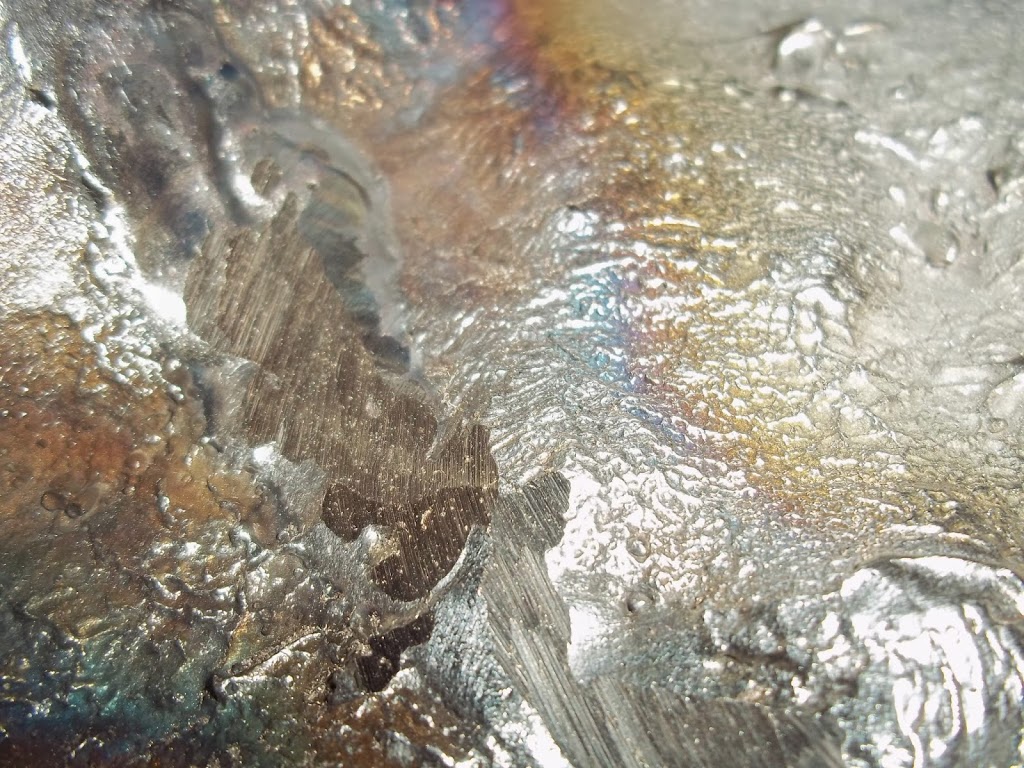
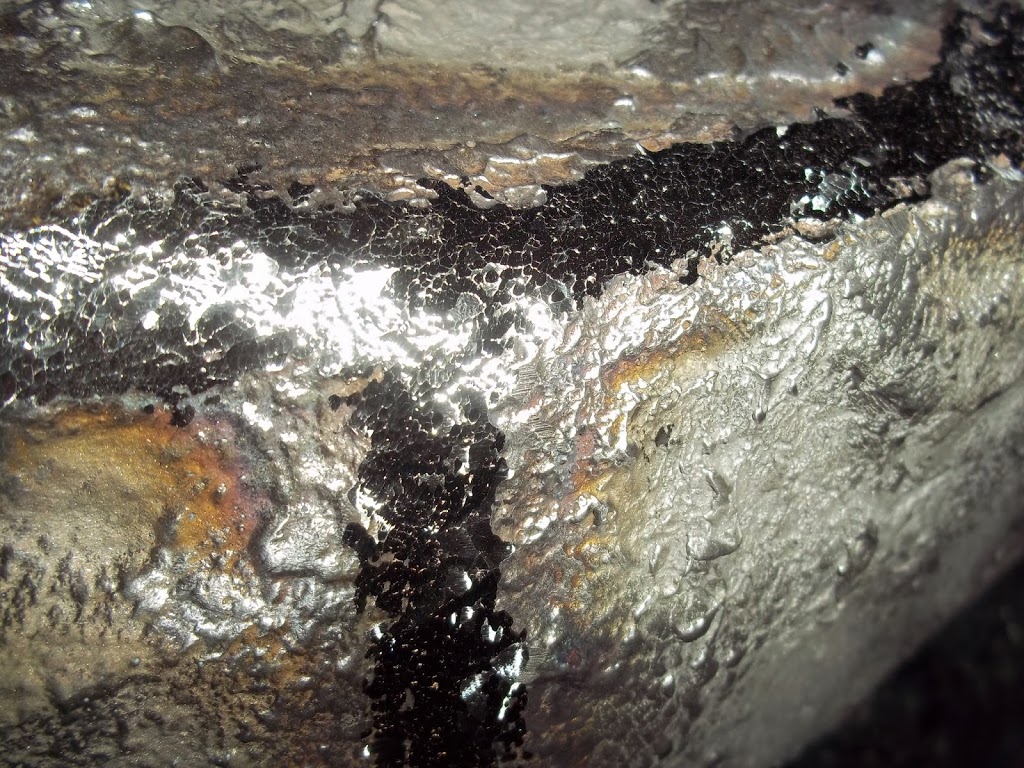
Removing The Ceramic Shell From The Tiger Head
In the post we saw some the process of pouring the head of the tiger. Now that the head is poured, the ceramic shell must be broken off of the metal. This is called divesting. I asked the foundry to take a movie of this part. It looks brutal, but it is important. If you watch the entire thing be sure to look at the how they also much take the shell of the inside the sculpture.

The second part of this video shows them taking the metal spurs off of the sculpture. I especially like the look of this video. Seeing the light from the torch shine through the holes in the sculpture.
Now, this piece will need to be sandblasted to get all of the ceramic shell off of the metal.
That Is One Hot Tiger! Pouring The Tiger Head
I could not wait to show you all this video. Here is a spectacular video of the pouring of the tiger head that was provided to me by Shidoni Art Foundry in New Mexico. They report that the tiger is coming along. This is the last piece to be cast in metal and has you have seen by previous posts it is coming along nicely. We will not have it there for homecoming, but will be delivering it later in November. I can’t wait to see it all together. More news later. Until then check out the pouring of the Tiger head.
VIDEO NOT AVAILABLE ON THIS PAGE- IT does show up on the Grambling blog page.
Rocking Out! Putting Together The Tiger Sculpture In Metal

There is still much to do with the tiger. If you have been reading this blog you have found that the process of creating a mascot is quite laborious. Here is the process with links, once again. Note: there are a lot of other posts of the process in between all of these links below.

- The First blog post –The beginning June 1, 2012 The blog begins.
- Design process June 17th – The designing and working on project begins long before the actually sculpting.
- Approval process January 23rd- Approvals and final paper work is received by client.
- Enlargement of Design January 23rd – The enlargement of the sculpture is being made into foam for us to sculpt on. Meanwhile we search for a warehouse to hold this big creature.
- Foam Armature arrives in Houston. The CNC milled foam gives us an armature to sculpt on and arrives in Houston in March
- Approval of Sculpture May 27th post. Which means we have sculpted this huge cat in 2 months! this would never be able to be done without the digital technology of CNC milling to enlarge the foam pieces. It is a huge accomplishment. There were many interns who worked endless long hours.
- Mold making The sculpture comes a part and we begin the first part of the foundry process the mold making.
- Molds shipped to Shidoni art Foundry July 27th They will finish the foundry process.
- Wax and Sprues or gates Beginning in August the Foundry makes waxes from the molds.
- Pouring of metal- The pouring of metal happens each weekend at Shidoni art Foundry.
This is what we have accomplished thus far. In the next few weeks the last steps will take place
- Welding
- Patination
- Delivery
- Installation
Here you can see that the many, many bronze pieces that are poured are now welded together.

Update
Someone pointed out to me today that this blog has not been updated in over a month.
I’m so sorry.
What I have been up to.
While Shidoni Foundry has been busy working on the tiger, I have been very busy with my own creative endeavors. For the last few months I have been putting together 3DCAMP Houston. 3DCAMP Houston. is a day long symposium on everything 3D. It crosses disciplines such as oil and gas, engineering, computer graphics and others. It is also used with my own passion- art. I am co chair of 3DCAMP Houston which was a marvelous success held at the University of Houston Architectural Department. It was a huge undertaking, I was also a speaker. My lecture was on Copyrights, Ethics and Responsibilities of 3D. I have been writing a book about 3D technology and fine art and craft and this lectures is from of my chapters.
I’m also happy to report that the Grambling Tiger head was displayed in the art gallery at 3DCAMP Houston. The art could be displayed because the show consisted of art that was created using some form of 3D technology. As you know by reading this blog, the tiger was first sculpted in the computer and then later it was CNC milled as it was enlarged, and then clay was added.
The Tiger update
I have spoken to both Grambling and Shidoni Foundry it is confirmed, that the tiger will not be at homecoming. Instead, I hear there will be a separate celebration at Grambling for the installation of the tiger.
I have been waiting on some more photographs and a video from Shidoni Foundry. I can’t wait to post those. I think they will be coming any day now. The entire tiger has gone through the casting process. The last piece that I was waiting for was the head. Now they have to put this puzzle piece together, create an internal armature and give it a patination. I am scheduled to come to Shidoni Foundry around the 11th of November. I will be monitoring the tiger the entire week at Shidoni. I’m not allowed to post pictures of the entire tiger together, until after the unveiling, but I’ll be sure to post some glimpses. The tiger, at this date, is scheduled to leave Shidoni Foundry on the 18th. It will be traveling in an open bed trailer from New Mexico to Louisiana. I wonder if anyone will spot it going down the highway?
Stay tuned for more information concerning the installation and celebration of the tiger.
Getting Ahead!
The foundry is saving the best for last on the Grambling State College mascot. I am so glad to see the head finally going into wax. Of course, this is just the wax, but that means from wax it goes to bronze. I have heard that all of the many wax pieces will be through the wax department at the foundry very soon. That is a huge milestone. If you have been following the process you can see that there is a lot of work that goes into the making of a mascot for a university. The workers at Shidoni Foundry rock!
We still do not know when the tiger will be delivered.

on a bronze is only as thick as the wax that is painted.

they are put together.
![]() |
Remember the wax head still needs a pour cup and sprues. A fangless grin from the tiger. And no ears. They are made separately and added later. |


YEA! We Have A Pour On The Grambling Tiger

The Grambling Mascot.
If you have been following the foundry process up to now, you have learned about
* The mold making that we did in May, June and July
* The waxes
* The gating up process and dip
* The burn out
and now we get to the exciting thing…. The pour.
When I dropped off the molds for the tiger at Shidoni in NM you may remember that I stayed at Bishops Lodge. I heard people at Bishops Lodge talking about the pour at Shidoni. Apparently Shidoni make this a regular Saturday event and people can come from the local hotels and watch.
A few weeks ago, I was on Facebook and heard that Susan Herndon was performing in the gardens at Shidoni. Then I saw a photo on Facebook of an empty bench with guitar and amps near by. I think the caption on the photo said, “stopping the music to see a pour.” I commented, and sure enough, it was our tiger.
The pour on the tiger will happen many times in the next few weeks. For every wax, that is gated up and burned out there will be a pour of the metal into those pieces. So here are some recent pictures from Shidoni concerning the tiger. I have asked if they can video tape the head being poured. I can’t wait to see that. So stay tuned.

the look of this molten bronze.

wax burned out of them. Now that cavity where the wax
once was will now be filled with molten bronze.
The men wear protective clothing.

that have been or will be- made into wax from the molds, gated up,
burned out, and poured. And we still have a few more steps after this.