Education
Giving A Hand To Someone In 3D Printing
I’m presently at 3D printing World Expo in Burbank California. I am speaking here on 3D technology and art. Speaking on day two of a conferences give you a chance to check out what others are doing and meet individuals. I have enjoyed doing just that. While here to speak I visited the key note presentation and was very impressed with Mick Ebling. Mick is from a company called Not Impossible. Mick went to Sudan and created what “is probably the world’s first 3D-printing prosthetic lab and training facility. More to the point of the journey is that Mick managed to give hope and independence back to a kid who, at age 14, had both his arms blown off and considered his life not worth living.” The video tells the story.
On the panel was also Mark Setrakian, who brought out a very impressive 3D printed mechanical hand/arm from what looked like the movie Hell boy. When he was done Mick asked Mark if he could make the model open source. Of Course Mark said he could not because it belonged to the movie industry, and Mick said one of the best lines of this conference. I will do my best to quote him “Depending on your religious beliefs, You can’t use IP about the functionality of a hand” It should be open source and available to everyone.
I am thrilled to help share the technology of 3D printing with as many people as I know. I am honored to be in the presence of those who take this technology and use it for the good of people. Mick, let me give you a hand, a standing ovation and a prayer that you continue in your good work.
_______________________________________________
Bridgette Mongeon is a sculptor, writer, illustrator and educator as well as a public speaker.
Her blog can be found at https://creativesculpture.com.
She is the vice chair of the planning committee for 3DCAMP Houston 2012 and 2013 http://www.3dcamphouston.com
Follow the artists on twitter twitter.com/Sculptorwriter
It Will Blow Your Mind!
Yes, I’m writing a book called 3D Technology in Fine Art and Craft. It is based on my graduate thesis on art and technology in the traditional studio. I have been gathering information for years and talking to many vendors and individuals who are leaders in 3D technology. All I can say is…
You don’t know what you can do,
until you know what you can do.
When you find out, it will blow your mind.
Picture this…
A book that does the following;
- Inspires through interviews with artists and craftspeople all over the world. Artists who are pushing the envelope with using 3D technology in fine art and craft. The interviews not only inspire you with multiple photographs, but the artists share a list of their vendors, software etc.
INSPIRATION!
- Thinking of trying the incredible technology of 3D Printing. Should you buy a printer, or use a service bureau, and if so which one. What do you need to know to get your feet wet?
Traditional artist wants to dabble in 3D technology. Where do I begin?
- Are you a traditional artist thinking of taking the plunge and incorporating 3D technology in your own at studio, but don’t know where to begin or even if it is applicable?
- Are you a traditional sculptor that would like to be able double or triple your income by giving you time to create instead of working 1/2 of your career making monumental armatures?
- Are you a CG artist and would like to realize your art in a physical form?
- Want to learn more about, CNC milling, or creating a holographic painting?
I have just tripled my income!
- Would you like a one stop resource list of 3D vendors and materials?
This is just a sample of what is in the book.
Not sure of publication date, more to come.
_______________________________________________

Bridgette Mongeon is a sculptor, writer, illustrator and educator as well as a public speaker.
Her blog can be found at https://creativesculpture.com.
She is the vice chair of the planning committee for 3DCAMP Houston 2012 and 2013 http://www.3dcamphouston.com
Follow the artists on twitter twitter.com/Sculptorwriter
From 3D Printing To CNC Milling
I’m diligently working on the new book 3D Technology in Fine Art and Craft. I have been plugging away at the 3D printing chapter for almost 2 months now, and I’m glad to say, it is almost done. At least the technical parts are. I still need to contact a vast number of vendors and artists and get release forms and photographs. I timed the completion of this chapter with my lectures that will be given at 3D Printer World Expo 2014. January 31 Feb 1, 2014. I hope to schedule some appointments with vendors while in Burbank and I’m sure I will find a variety of things to add to this chapter upon my return.
When I’m not writing, I’m bidding on projects and doing designs for my own work that will take place in the traditional sculpture studio. These designs are usually started in 3D in the computer. As I push the limits both of the technology and the driver of this technology, myself, I have a ton of questions, problems many that need immediate solutions so that I may proceed.
My work is not like most that are working in 3D on the computer, or shall I say the outcome is not the same. I need to realize my work in physical form. I’m usually challenging the 3D guru guys. But some of my vendors, and cohorts in the tinkering of art and technology often share some of the coolest products and software. Thanks once again Steven Ramariz with Smash Designs. I’ll be getting some of these products and software to try for the book, and some of these are in CNC milling.
As I finish this chapter of 3D printing, I’m chomping at the bit to get going on the CNC milling chapter. There are some pretty cool things to share. I know I won’t be able to hold it all in while I’m writing. So, expect to seem some posts here that reveal a bit of these treasures.
_______________________________________________
Bridgette Mongeon is a sculptor, writer, illustrator and educator as well as a public speaker.
Her blog can be found at https://creativesculpture.com.
She is the vice chair of the planning committee for 3DCAMP Houston 2012 and 2013 http://www.3dcamphouston.com
Follow the artists on twitter twitter.com/Sculptorwriter
Pushing The Limits and Size of Fine Art And 3D Printing
I have been a fan of Eric van Straaten’s work for a while now. I found his work by doing research for the book that I am writing titled 3D Technology in Fine Art and Craft. I am thrilled that he has agreed to be one of the featured artists for the book and to share his process. As most of you know, the reason that I am writing this book is that I have been exploring and using a combination of technology and traditional art for a while now. I have reported on it in several magazines. Also, fine art and technology is what I received my degree in back in 2012.
The technology is constantly changing, and I have to spend a lot of time to keep up with it. That is why I hope that the book 3D Technology in Fine Art and Craft will become a series and repeat in the future, introducing the latest in technology and new artists who are pushing the limits. Of course, that will depend on my time and the publisher allowing for future editions, but first I need to complete this one, and there is a lot of research involved.
Now on to Eric’s work.
Because I have been a fan of Eric’s work, I have signed up for Eric’s email newsletter. I love to hear what he is doing. Basically, Eric has been creating fine art pieces through 3D printing. What intrigues me about Eric’s work is that the is not just 3D printed artwork in plastic, but instead the pieces are 3dD printed in color He is just not “manufacturing” work, but selling them as fine art. I have often stated that the themes of Eric’s work are a little risque, but in a way they are charming and the soft almost sugary look that printing in color on the ZCorp 650 gives a sweetness and innocence to the piece that I don’t think would be there in another medium.
Again Eric pushes the limits, this time with size. You see the ZCorp 650 can only print 37 x 25 x 20 cm , which is approximately 14.5“ x 10 x 8 inches. So Eric created 10 different interconnecting parts that are glues together. Also, the ZCorp 3D printed parts are not the strongest pieces to work with, that is why they are strengthened. Eric says “they are probably stronger than you think, comparable to ceramics.” But still, he is nervous about transporting them.
I can’t wait to interview all of these creative and wonderful artists for the book, and I’m so thankful they are going to share their process, vendors and materials with us through 3D Technology in Fine Art and Craft. Apparently I’m not the only one who is into inspiring and encouraging the marriage of fine art and technology.
Eric’s work will be exhibited at the art fair REALISME in the Passenger Terminal in Amsterdam.
_______________________________________________
Bridgette Mongeon is a sculptor, writer, illustrator and educator as well as a public speaker.
Her blog can be found at https://creativesculpture.com.
She is the vice chair of the planning committee for 3DCAMP Houston 2012 and 2013 http://www.3dcamphouston.com
Follow the artists on twitter twitter.com/Sculptorwriter
Need Help With This Part Of A Chapter- 3D Printing And Investment Casting
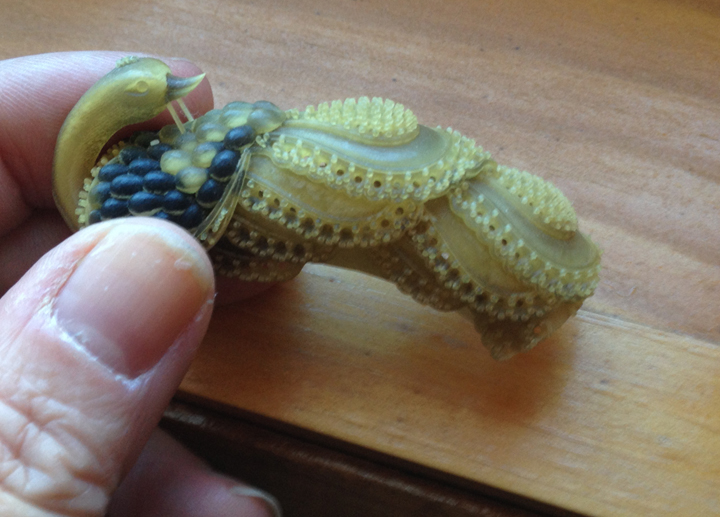
I spend a lot of time on the internet searching for new technology or posting comments on my groups on linkedIn. I am writing a book about using 3D technology in both fine art and craft. I’m putting some of my questions and thoughts below. Please feel free to add to them with things you have discovered, correct my errors in the technological processes, and when possible cite your comments or background. Please let me know if I may quote you if that applies. Also, I’m looking for examples with incredible art. I’m not into showing the creation of oil valves or common items, though that may be what some of these processes are made for. If you have samples of artists or art using these processes, please contact them and see if they would like to be featured in the book and then let me know. I would love to hear about their processes. If you are interested in having an artist try your products to be featured in the book, contact me and I’ll either use my own work, or if I am busy writing, pass it on to another artist that I want to feature, and whose work is top notch.
Investment casting and 3d printing.
Today my search leads me to the topic of 3d printing and investment casting. I’m going to summarize some of my questions in this post and then send this around and hope that some professionals in the industry will be able to help me. It is also my hit list of professionals and companies that I am trying to reach. (Not an easy job as I am presently writing from New Mexico instead of my home base in Houston, Texas, and I do not have my hit list here. This NM trip is another story all together.)
Many things can be burned out of an investment casting. The things I’m noting when discussing these processes of burning out are; detail, a clean burn, temperature, cost, toxicity and build envelope. The few things I am covering in this section of this chapter are listed below. If there are some I have forgotten please feel free to let me know.
ABS and PLA-
Of these I know that PLA is preferred because of the toxicity of ABS. I also have the extrude temperature of ABS as 225 and of PLA 180-200 I suppose this will also depend on the supplier of both materials, but in general is this correct? If this is the extrude temperature what would be the burn out temperature for investment casting?
ABS
* Detail—
* Clean burn?—
* Temperature—
* Cost—
* Toxicity—
* Build envelope–
* Machines and stats and service bureaus and stats–
PLA
* Detail—
* Clean burn?—
* Temperature—
* Cost—
* Toxicity—
* Build envelope–
* Machines and stats and service bureaus and stats–
PAPER AND CERAMIC
In a podcast interview with fellow artist Paul Effinger we talked about burn out quite a bit. But this interview and the accompanying book that I wrote, “Digital Sculpting With Mudbox: Essential Tools and Techniques for Aritst “ with Mike de la Flor showed his work. I believe that his piece “Artifices” was 3d printed with a ceramic powder and dipped in a resin binder. The piece, that we featured on page 187 of the Mudbox book, was apparently printed on a ZCorp510. OK 3Dsystems. So, any updates on systems doing this and details.
The Mudbox book was written in 2009 and printed in 2010 and was one of the first books to feature a chapter on 3D technology in the art. I’m curious how the technology has advanced. What machines and service bureaus are printing paper or ceramic for burn out. How do they compare with the detail, a clean burn, temperature, cost, toxicity and build envelope?
I know that mcor technologies is doing some great printing with paper. I’d like to feature them in another part of the book because I love the color work, but I’d also love to talk to them about investment casting and 3D printing of paper.
With these products it appears that many are dipped into a solution. If your product is dipped please clarify what it is dipped in and why. Also, as an artist I am concerned if a piece is dipped in anything as I know that the dip will really affect the texture on a piece. I love texture on my artwork and this would be very difficult for me.
Also, with all 3d printing texture is more than just what I put into it, but what the material that is being burned out can affect the look of a piece . I have created molds from wet clay, dry clay, and oil base clay and the same figure will look totally different depending on the item being molded. I’m interested in investigating this more with the 3d printing.
WAX
I’m pretty impressed with what I have seen with the wax 3d printing. This piece was sent to me from 3D SYSTEMS a few years ago. I love the detail and take it with me on all my lectures to show as an example. Going to have to dig in my contact list when I get back to the office to find out who sent this to me, and what machine it was printed on. This definitely is an example of the quality/detail that I am trying to show in this book. So what machines are printing wax for investment casting? How do they compare?
I also loved what I saw at envision tech and would love to find someone from this company to talk to.
* Detail—
* Clean burn?—
* Temperature—
* Cost—
* Toxicity—
* Build envelope–
* Machines and stats and service bureaus and stats–PAPER AND CERAMIC
.MGX by Materialize.
I know that .MGX by Materialize has been working on a large build envelope and investment casting. I won’t describe it here, but when I interviewed Joris Debois back in 2010 , we talked about it. We were in contact about 2 weeks ago. I look forward to hearing from.MGX by Materialize. Their process will be a major section in this chapter.
* Detail—
* Clean burn?—
* Temperature—
* Cost—
* Toxicity—
* Build envelope–
* Machines and stats and service bureaus and stats–PAPER AND CERAMIC
Thank you for everyones help. Please feel free to respond here or on linked in, or contact me and let me and we can set up a time to chat if necessary. Thanks in advance,
Bridgette Mongeon
Also note: This section is just about burn out. I am also interested in other parts of 3D technology that are entering or may influence the traditional process of fine art bronze casting, such as what is mentioned in the American Article that I wrote for Sculpture Review in 2007. I’m going to hit up exone and Bob Wood again about printing the investment instead of the piece for investment. I’m wondering how that has changed over the last few years. The 3D printing in metal is discussed in another section.
An Encore of “Taming The Beast” Presentation
I’m in Sata Fe this week checking the progress on the Grambling State Louisiana Tiger. While here, I presented a lecture called Taming the Beast: 3D Technology in Fine Art and Craft. In the lecture I spoke about the creating of the tiger, how 3D technology is advancing, and how artists are using 3D technology in their workflow. The lecture features a modified and very shortened version of what will be in my new book, 3D Technology in Fine Art and Craft. Shidoni Foundry hosted the first Santa Fe lecture.
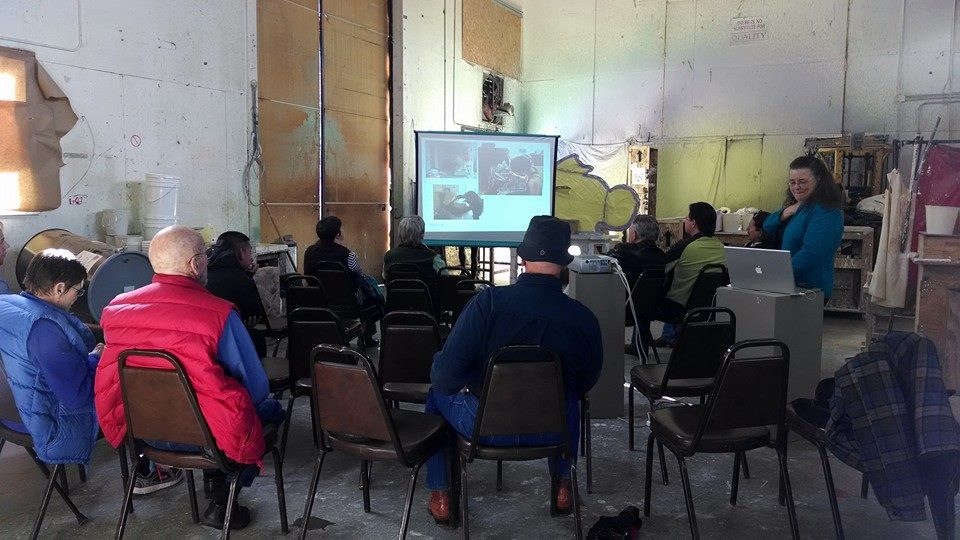
I gave the second presentation of Taming the Beast at a private gathering at Mary Anne’s Stickler’s home. Mary Anne is my host while in Santa Fe and has opened her lovely home to me.
There has been discussion about doing yet another repeat performance of the lecture while I am here. I have extended my stay, and I am in town until the 27th. If we can schedule this, I’ll let everyone know the date, place and time – probably through this blog post or Facebook, so feel free to like my Creative Sculpture facebook page, and comment here on this blog post or on Facebook about the best dates for you, and if you would like to attend. We don’t need a big crowd, 8-20 people is fine.
I will also state that for those people who have heard the lecture, you might also be interested to note that Shidoni Foundry has regular bronze pours on noon on Saturday. If you have never seen this take place it is breath taking. Here is a video they helped me create when they poured the tiger head. Give them a call to reserve your space,1508 Bishop’s Lodge Rd., Tesuque, New Mexico 87574 (505) 988-8001. You can also request to see the beast.
If enough people are interested, and Shidoni is agreeable, maybe the repeat performance can be done there on Saturday morning, before or after a pour. Let me know your preferences, I’m also open to another venue if someoone has suggestions.
For future reference, a Santa Fe artist asked if I would come back and do the lecture in Albeququerqe in the Spring, he is organizing it. I’m delighted. If you know of anyone in Albuquerque that might like to be a part of this as either and attendee, sponsor or would like to host, please let me know I’ll pass the information on to him.
IF YOU ATTENDED EITHER LECTURE
I would greatly appreciate your comments. Please feel free to post them below. Please note, if you comment you are giving me permission to use these elsewhere. These comments are very valuable for me because they help others get a feel for a lecture. For example two that I use quite often concerning my Marketing in the Arts workshop state:
“This workshop is a necessity for every practicing artist and student. I commend Ms. Mongeon on the development of such a resource. “
Professor David Hickman University of Houston
Former President-Houston Society of Illustrators
“I left the room with the certainty that if fame and fortune were going tobe mine, it would only occur if I took the bull by the horns, and you showed me not only where the bull was but how to get the horns, as well.
Besides your ebullient enthusiasm, which is highly contagious, you also shared with us lucky attendees really practical steps to getting where we want to go. I left the lecture with a suitcase of ideas.”
Mary Erbert
Artist-Houston
IN CLOSING
I would like to thank everyone in Santa Fe for their warm welcome and excitement over my work and my research. if you have attended Taming of the Beast: Using 3D Technology in Fine Art and Craft , please feel free to comment here and and include your name and title and location, also let me know what you think about a time , date and place of a repeat performance of the lecture.
Private Gathering on Art and Technology

shared information about incorporating
3D technology in the traditional sculpture
studio at Shidoni Foundry. The lecture
culminated with a viewing of the cast
sculpture and a foundry pour.
As many of you know, I am in New Mexico approving the sculpture of the 14+ foot bronze tiger that I created for Grambling State University in Louisiana. It is being cast by Shidoni Foundry. I also gave a presentation at Shidoni Foundry titled Taming the Beast: A Lecture on Fine Art, Craft and Technology. The lecture is about the process of creating the tiger, but also about some of the items in the new book that I am writing titled 3D Technology in Fine Art and Craft.
My very gracious hostess here in Santa Fe, Mary Anne Stickler has offered to have private gathering in her home for some of her friends who are interested in art, and great conversation. I’m so honored.
Date: Monday, November 18th
Time: 4:00 p.m.
If you miss either one of these lectures and gatherings, don’t fret. I’ll be back this spring doing something similar in Albuquerque-details to come. Oh, and if you want me to come and speak in your area, just give me a call.
_____________________________________________

Bridgette Mongeon is a sculptor, writer, illustrator and educator as well as a public speaker.
Her blog can be found at https://creativesculpture.com.
She is the vice chair of the planning committee for 3DCAMP Houston 2012 and 2013 http://www.3dcamphouston.com
Follow the artists on twitter twitter.com/Sculptorwriter
Taming The Beast: A Lecture On Fine Art, Craft And Technology

Taming the Beast: A Lecture on Fine Art, Craft and Technology
Sculptor Bridgette Mongeon will be presenting a lecture on incorporating digital technology in traditional art and craft on Saturday, November 16, 2013 at 10:00 at Shidoni Foundry, 1508 Bishops Lodge Road, Tesuque, NM 87574.
Digital Sculpting, CNC milling, and 3D printing, combined with traditional sculpture, is the way that Bridgette tamed the 15’ tiger that she sculpted for Grambling State University. Shidoni Foundry in Santa Fe, NM is casting the beast!
Bridgette will be discussing the technology, her process and how others are combining the technology in art, craft and science. The creative event will culminate with a viewing of the completed bronze tiger and a demonstration of a Shidoni bronze pour. Space is limited. To reserve space for Taming the Beast contact Shidoni Foundry office, 505-988-8001 ex 114
About the Artist
Houston, Texas sculptor, Bridgette Mongeon, is a traditional figurative sculptor of over 30 years. Bridgette began to incorporate digital technology in her work in 2008 and coauthored the book Digital Sculpting with Mudbox: Essential Tools and Techniques for Artists. Writing and lecturing about; art, marketing in the arts, creativity, and digital technology, gives her great pleasure. Bridgette holds a BA from Vermont College and an MFA from Goddard. She is presently working on a new book about 3D technology in art and craft.
_____________________________________________

Bridgette Mongeon is a sculptor, writer, illustrator and educator as well as a public speaker.
Her blog can be found at https://creativesculpture.com.
She is the vice chair of the planning committee for 3DCAMP Houston 2012 and 2013 http://www.3dcamphouston.com
Follow the artists on twitter twitter.com/Sculptorwriter
3D Technology in Art and Craft – A Question- 3D Printing in Color
I’m working on a new book that details 3D technology in Art and Craft. It will describe how to create art using such things as 3D printing, 3D scanning, 3D sculpting and 3D milling. It will show how to combine these technologies with traditional art and craft. It will also contain interviews with businesses and artists to discuss their processes. Finally it will be a one stop book that features vendors and other resources.
I’m culling through my many years of research and writing on this topic. I studied 3D technology as it is combined with art as my MFA, and have written and lectured on this topic often. I’m also looking at the new technology that is coming out. In light of that, I thought I would post some of my own questions on the topic. If you have an answer to these questions please feel free to post in the comments section of the blog or drop me a line. Please cite your answers when possible. I greatly appreciate it.
3D Question- printing in color.
I’m intrigued with printing in color.
As part of the book I really want to walk the reader through creating a piece of art that uses 3D scanning and 3D printing as the art interacts with natural surroundings. I wrote about that in a previous post. I love the video created by Greg Petchovsky who takes objects in the real world and then recreates them or adds to them in a 3D program and then prints them out using a 3Dprinter. I contacted Greg about this project, asked him how he scanned the color and what other details he could tell me about the quick projects in the video. He was kind enough to answer some questions. Here are his comments from the e mail
had my prints done by Shapeways, they used ZCorp 3d printers.
The material isn’t waterproof, it will warp and develop white discoloration if exposed to water. I haven’t left 3d prints outside for a long period of time, so I’m unsure how long they would hold up.
I set up the scale in 3ds Max. I just used calipers to measure the object, but in future I’m thinking I’d include a wooden ruler in the scan.
I don’t think I’d use masks or visibility to make meshes fit into each other. I’d try to use booleans. I haven’t experimented all that much with booleans in zbrush, but basically there’s a button over each subtool that lets you chose between additive, subtractive, or intersection. And the resulting mesh can be calculated using the “remesh all” button… though the results might be somewhat mushy. I believe similar (possibly better?) results can be achieved with dynamesh? And I guess the details could be re applied using projection.”
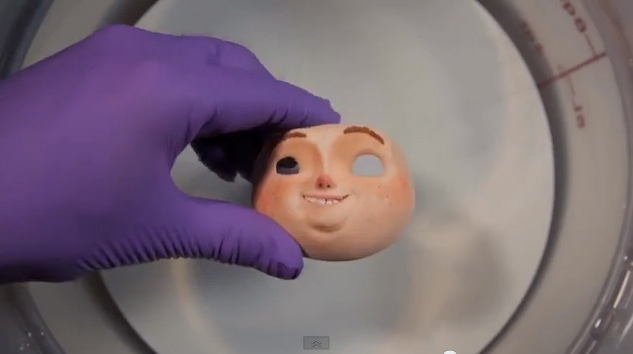
I am also intrigued with the work of Laika and how the puppeteers created the pieces for the making of the movie Paranorman. Each puppet was created using different expressions. These expressions were used with stop animation and some computer graphic work to create the film Paranorman. I’m assuming the super glue will help to strengthen the piece as well as keep it clean.
It is reported by the University of Texas at Austin Architecture school, in this article that using super glue can double the price of a 3D printed piece. I’m still not certain what the process is of “dipping” a piece in super glue/acetone. Seems like it would make a mess and be very difficult to handle. I can’t believe no one has figure out another way to harden these materials. Also, it looks like none of these things printed in color can be used outdoors, so I may have to modify my example for the book to use drift wood instead.
I contacted one of my go -to people on 3D printing Paul Cesak, who just happens to also be the guy that started the 3D printing group on linkedin. The 3D printing group is growing by leaps and bounds. He replies “only with 3D Systems can a 3D print have the full spectrum of color. The downside of that is that it is printed on plaster, is very fragile, and has the texture of sand. Indeed small details are either not printed or are lost in the post-processing.”
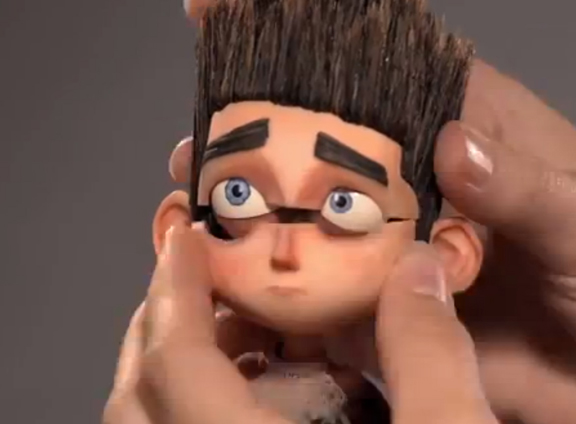
I contacted one of my go -to people on 3D printing Paul Cesak, who just happens to also be the guy that started the 3D printing group on linkedin. The 3D printing group is growing by leaps and bounds. He replies “only with 3D Systems can a 3D print have the full spectrum of color. The downside of that is that it is printed on plaster, is very fragile, and has the texture of sand. Indeed small details are either not printed or are lost in the post-processing.”
Another artist that I will be interviewing for the book is Eric Van Straaten. This video shows his work being created. I’m not sure he uses anything to strengthen his pieces. I’ll let you know after we talk for the book.
I have many questions.
QUESTION: how does an STL translate color? I though STL files did not have color?
QUESTION: What 3D printers can print in color?
QUESTION: If this is done through SLS printing, how does the laser depict color? ( I’m wondering if this can be explained simply)
QUESTION: is there nothing else that can strengthen the pieces using this type of 3D printing?
_____________________________________________

Bridgette Mongeon is a sculptor, writer, illustrator and educator as well as a public speaker.
Her blog can be found at https://creativesculpture.com.
She is the vice chair of the planning committee for 3DCAMP Houston 2012 and 2013 http://www.3dcamphouston.com
Follow the artists on twitter twitter.com/Sculptorwriter
Come And Put Your Head In The Mouth of A Tiger
My work has been accepted into the 3DCAMP Art Show! Well not all of it just the head!
I have just discovered that my tiger will be at the 3DCAMP event scheduled for October 5th. WHAT? Well not the entire 15 foot tiger, but the head. I’ll also have information that demonstrates the 3D process used in making this. You really should come by and see it, and have a picture taken with it.
No baby sacrifice is required, just sign up for a day of fun and brain stimulation at U of H. Here is the website. Oh, and tickets are limited so sign up today. And when you interact with this thing please send me some photographs so I can post them here!
If you would like to see the entire tiger visit the Grambling University Tiger Project blog where I am documenting the entire process. Check out the beginning of the blog to see the digital creation and learn about the CNC milling used to enlarge this beast.
Bridgette Mongeon is a sculptor, writer, illustrator and educator as well as a public speaker.
Her blog can be found at https://creativesculpture.com.
She is the vice chair of the planning committee for 3DCAMP Houston 2012 http://www.3dcamphouston.com
She is also the owner and creator of the God’s Word Collectible Sculpture series http://www.godsword.net
Follow the artists on twitter twitter.com/Sculptorwriter and twitter.com/creategodsword
Listen to The Creative Christian Podcast or the Inspiration/Generation Podcast
Click on Podcast Host Bios for a list of all podcasts.